Asphalt Plants
Existing Plants Add Recycling Capabilities
A Chinese road builder is planning to add recycling capabilities to existing asphalt-mixing plants to meet new environmental guidelines – and substantially reduce costs, too.
CSCEC Road & Bridge is a highly successful business by virtually any criteria. It has won more than 20 national and provincial awards and has completed more than 1000 key projects globally. Its parent company is ranked 26th in the Fortune Global 500.
CSCEC Road & Bridge utilises Ammann Uniglobe Asphalt-Mixing Plants, and the results have been impressive. During one key road expansion, a Uniglobe plant produced 7000 tonnes in a single day, and averaged 5000 tonnes per day during the project. Both numbers are thought to be all-time production highs for China.
Yet success in China is increasingly defined by more than production. “In recent years, as more and more public-private partnerships are coming out, we also are paying more attention to recycling technology,” said Mr. Zhou Shixin, chairman of a CSCEC Road & Bridge branch in Shijiazhuang City.
The company owns four productive Ammann Uniglobe plants that have a great deal of life left in them. That has led CSCEC Road & Bridge to plan to add recycling capabilities to those existing Ammann plants
Ammann is an expert in upgrading the plants, and has a proven process for doing so.
The improvement includes the addition of an RAH drum that heats the RAP before depositing it in the mixer. RAP needs the separate RAH drum because it must be gently preheated. This is because bitumen in the RAP is damaged when overheated. The bitumen is valuable, and preserving it is a cost saver.
After preheating, the RAP is deposited in the mixer, where it is blended with the hot virgin aggregate. The result is a quality mix with a high percentage of recyclables.
Ammann has a great deal of experience in making the plant upgrades, and often is able to complete the work in the off-season.
Adding the RAP capability is considerably less expensive than purchasing a new plant with recycling ability, Zhou said.
The company appreciates the green approach and the costs savings, too. “We can mill our own material for public-private partnerships and reduce costs by 20 per cent to 30 per cent,” Zhou said.
CSCEC Road & Bridge is a highly successful business by virtually any criteria. It has won more than 20 national and provincial awards and has completed more than 1000 key projects globally. Its parent company is ranked 26th in the Fortune Global 500.
CSCEC Road & Bridge utilises Ammann Uniglobe Asphalt-Mixing Plants, and the results have been impressive. During one key road expansion, a Uniglobe plant produced 7000 tonnes in a single day, and averaged 5000 tonnes per day during the project. Both numbers are thought to be all-time production highs for China.
Yet success in China is increasingly defined by more than production. “In recent years, as more and more public-private partnerships are coming out, we also are paying more attention to recycling technology,” said Mr. Zhou Shixin, chairman of a CSCEC Road & Bridge branch in Shijiazhuang City.
The company owns four productive Ammann Uniglobe plants that have a great deal of life left in them. That has led CSCEC Road & Bridge to plan to add recycling capabilities to those existing Ammann plants
Ammann is an expert in upgrading the plants, and has a proven process for doing so.
The improvement includes the addition of an RAH drum that heats the RAP before depositing it in the mixer. RAP needs the separate RAH drum because it must be gently preheated. This is because bitumen in the RAP is damaged when overheated. The bitumen is valuable, and preserving it is a cost saver.
After preheating, the RAP is deposited in the mixer, where it is blended with the hot virgin aggregate. The result is a quality mix with a high percentage of recyclables.
Ammann has a great deal of experience in making the plant upgrades, and often is able to complete the work in the off-season.
Adding the RAP capability is considerably less expensive than purchasing a new plant with recycling ability, Zhou said.
The company appreciates the green approach and the costs savings, too. “We can mill our own material for public-private partnerships and reduce costs by 20 per cent to 30 per cent,” Zhou said.
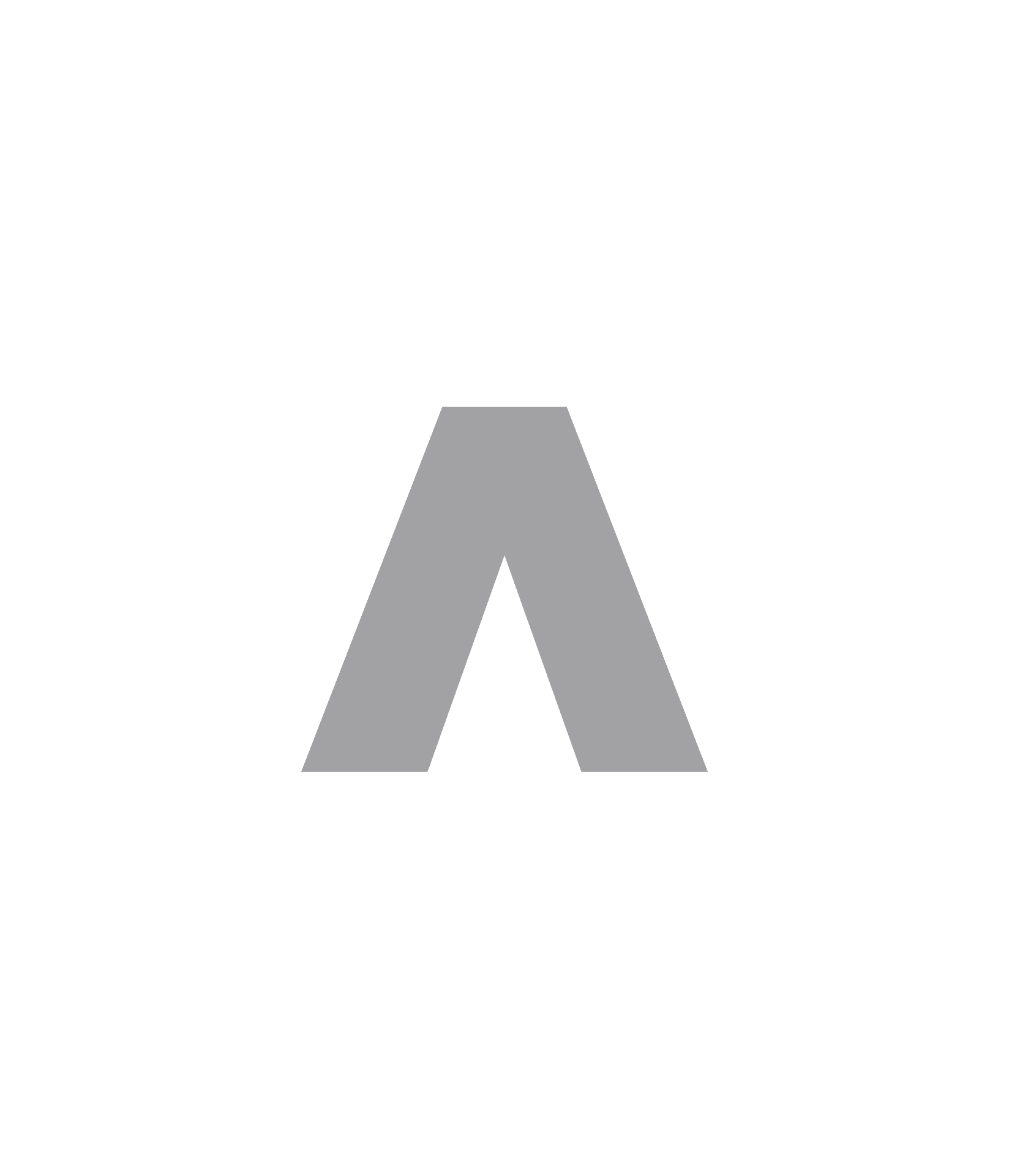
Contact Form
Schedule online meeting
Get in touch with us to meet a sales representative near you
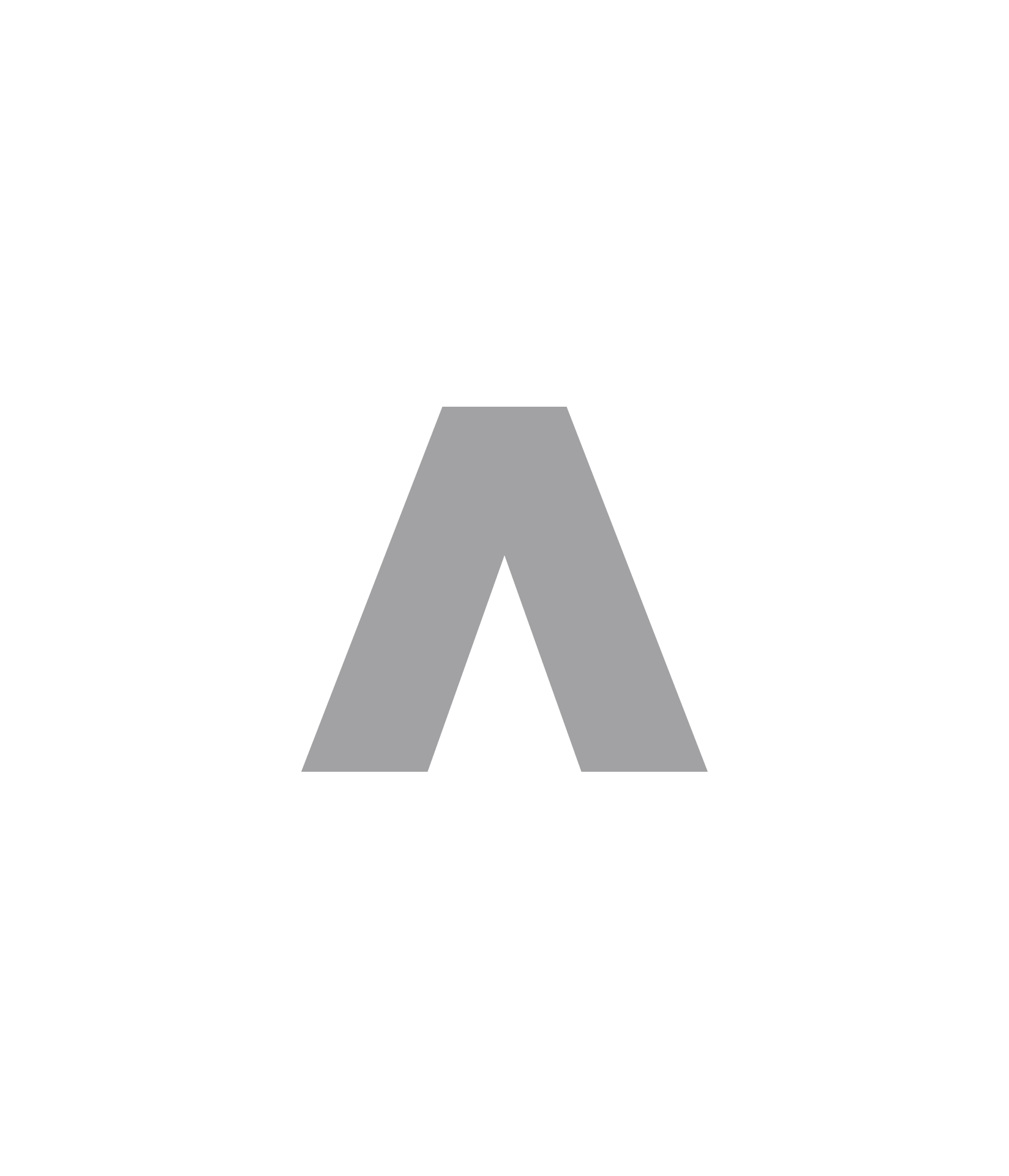