Últimas tecnologías e innovaciones
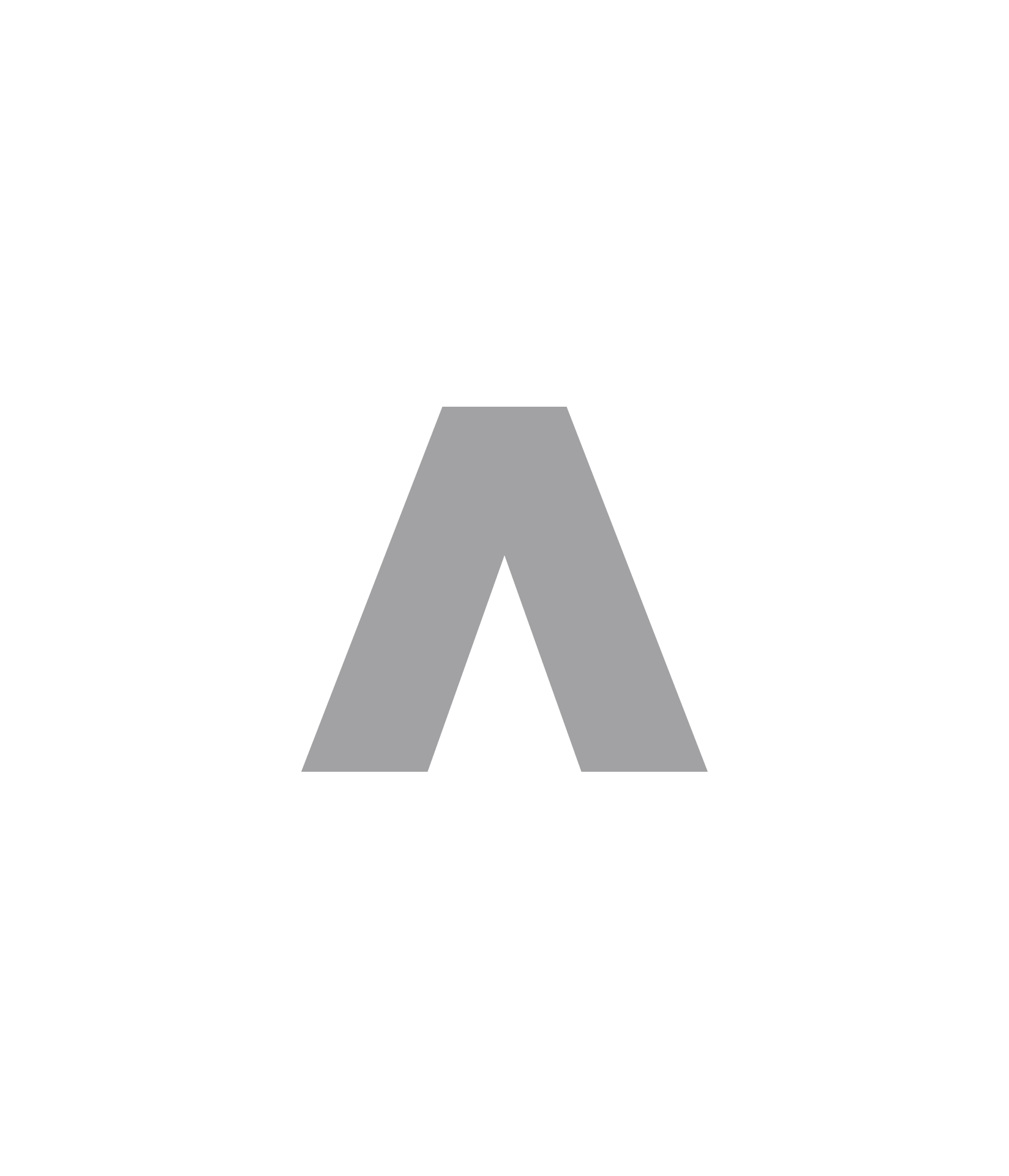
¿Cómo podemos usar menos, y cómo podemos hacer que lo que usamos dure más? Estas cuestiones son el núcleo de los esfuerzos de sostenibilidad de Ammann.
Examinamos a fondo nuestras instalaciones, máquinas y procesos existentes en busca de mejoras, por pequeñas que parezcan. Al fin y al cabo, cada paso que se da suma, es una lección que hemos aprendido en nuestros más de 150 años en el negocio.
¿Qué ha aportado este compromiso? Hemos conseguido reducir las emisiones en todas las plantas y máquinas, disminuyendo las necesidades de eliminación de fluidos y mejorando drásticamente la capacidad de reciclaje del asfalto, entre otros avances.