Postes d’enrobage
LES RETROFITS SONT UN PLUS POUR L’ENVIRONNEMENT
La réduction des émissions concerne également les émissions de poussières.
Il y a quatre ans, la société bavaroise Fiegl GmbH a investi dans une opération de retrofit pour la tour de malaxage de sa centrale d’enrobés.
Aujourd’hui, le système de dépoussiérage nécessite d’être remplacé. Le délai d’action était extrêmement court : en effet, il fallait éviter tout temps d'arrêt prolongé et toutes pertes de production en milieu de saison. Le remplacement devait donc se faire à l’occasion du long weekend de la Fête-Dieu au mois de mai de cette année. Après 20 années de fonctionnement, le démontage de l’ancien système de dépoussiérage a commencé en ce jour férié, et le lundi matin suivant, le test de la nouvelle installation débutait avec succès.
Grâce à ce nouveau système de dépoussiérage, la société Fiegl GmbH & Co. KG de Pleinfeld en Bavière dispose désormais d’une installation de production moderne qui, de plus, fonctionne de manière respectueuse de l’environnement. Cette mesure globale a permis de réduire de manière significative les émissions de poussière les nuisances sonores ainsi que les besoins en énergie.
Que ce soit principalement pour alimenter ses propres besoins ou des clients privés et publics, l’entreprise ne manque pas d’opportunités de produire des enrobés, et ce depuis de nombreuses années. Cette société, dirigée par la même famille depuis trois générations et installée au bord du Grand Brombachsee en Franconie centrale, propose toutes les prestations liées à la construction routière et au génie civil.
Elle dispose de plus des machines de construction correspondantes. Deux colonnes d’enrobés sont utilisées dans un périmètre de 50 km.
La première grande étape
En 2014, le poste d’enrobage datant des années 1970 a été remplacé. La tour de l’installation de type Universal 240 de la société Ammann culmine à 35 m de hauteur. Avec cette installation, la société Fiegl GmbH est en mesure de produire jusqu'à 1500 t d’enrobés par jour. Le silo de mélange a une capacité de
240 t et le silo des minéraux chauds une capacité de 120 t. Les granulats pour enrobés peuvent être alimentés à froid via l’élévateur. 2 réservoirs tampons pour différentes tailles de granulats sont également disponibles.
Le réservoir de bitume a de son côté également été mis au niveau technique. Deux ont été remplacés, un autre a été amélioré. Aujourd’hui, les deux réservoirs chauffés à l’électricité, et non plus à l’huile thermique. Le silo de filler a également été remplacé. Déjà lors de ces projets d’envergure, la collaboration entre les deux entreprises était excellente. Tout est réunion pour que ce soit de nouveau le cas dans le cadre de ce nouveau projet.
De bonnes expériences
Une bonne harmonisation était le principal facteur clé du bon déroulement du projet. En particulier « la réunion de préparation au montage » une semaine avant le début des travaux.
Toutes les personnes impliquées dans le projet se sont alors rassemblées pour discuter sur place de toutes les éventualités : chef de projet, ingénieurs, électro-techniciens, monteurs, responsables des commandes et bien entendu le chef de poste et les représentants de la société fournissant la grue. La mise en service réussie du système de dépoussiérage à la fin d’un week-end de travail bien rempli a prouvé la pertinence du processus.
Pour la prochaine étape
En plus de la réduction des émissions, du niveau sonore et des besoins en énergie, le nouveau système de dépoussiérage offre notamment des avantages grâce à des réserves sous pression et à sa sécurité de fonctionnement.
De plus, le système est équipé de manches de filtres Ammatex afin d’offrir une longue durée de vie. Ces machines de filtres résistent aux températures élevées et sont imprégnés de PTFE par défaut. Même les coutures sont en PTFE. Le polytétrafluoroéthylène est communément appelé « téflon », pour les tissus on utilise le terme de « Gore-Tex ».
Les manches de filtres rendent inutile l’utilisation de clapets d’air frais. Aucun air supplémentaire n’est requis pour le nettoyage des toiles. La stabilité de la forme des manches de filtres est assurée par thermofixation. L'installation de dépoussiérage de Pleinfeld de type AFA 3089 offre une puissance de 63’000 Nm./h et est régulée par un convertisseur de fréquence.
La surface de filtre est de 1045 m2. C’est largement suffisant pour répondre aux exigences environnementales du fonctionnement du poste d’enrobage.
Il y a quatre ans, la société bavaroise Fiegl GmbH a investi dans une opération de retrofit pour la tour de malaxage de sa centrale d’enrobés.
Aujourd’hui, le système de dépoussiérage nécessite d’être remplacé. Le délai d’action était extrêmement court : en effet, il fallait éviter tout temps d'arrêt prolongé et toutes pertes de production en milieu de saison. Le remplacement devait donc se faire à l’occasion du long weekend de la Fête-Dieu au mois de mai de cette année. Après 20 années de fonctionnement, le démontage de l’ancien système de dépoussiérage a commencé en ce jour férié, et le lundi matin suivant, le test de la nouvelle installation débutait avec succès.
Grâce à ce nouveau système de dépoussiérage, la société Fiegl GmbH & Co. KG de Pleinfeld en Bavière dispose désormais d’une installation de production moderne qui, de plus, fonctionne de manière respectueuse de l’environnement. Cette mesure globale a permis de réduire de manière significative les émissions de poussière les nuisances sonores ainsi que les besoins en énergie.
Que ce soit principalement pour alimenter ses propres besoins ou des clients privés et publics, l’entreprise ne manque pas d’opportunités de produire des enrobés, et ce depuis de nombreuses années. Cette société, dirigée par la même famille depuis trois générations et installée au bord du Grand Brombachsee en Franconie centrale, propose toutes les prestations liées à la construction routière et au génie civil.
Elle dispose de plus des machines de construction correspondantes. Deux colonnes d’enrobés sont utilisées dans un périmètre de 50 km.
La première grande étape
En 2014, le poste d’enrobage datant des années 1970 a été remplacé. La tour de l’installation de type Universal 240 de la société Ammann culmine à 35 m de hauteur. Avec cette installation, la société Fiegl GmbH est en mesure de produire jusqu'à 1500 t d’enrobés par jour. Le silo de mélange a une capacité de
240 t et le silo des minéraux chauds une capacité de 120 t. Les granulats pour enrobés peuvent être alimentés à froid via l’élévateur. 2 réservoirs tampons pour différentes tailles de granulats sont également disponibles.
Le réservoir de bitume a de son côté également été mis au niveau technique. Deux ont été remplacés, un autre a été amélioré. Aujourd’hui, les deux réservoirs chauffés à l’électricité, et non plus à l’huile thermique. Le silo de filler a également été remplacé. Déjà lors de ces projets d’envergure, la collaboration entre les deux entreprises était excellente. Tout est réunion pour que ce soit de nouveau le cas dans le cadre de ce nouveau projet.
De bonnes expériences
Une bonne harmonisation était le principal facteur clé du bon déroulement du projet. En particulier « la réunion de préparation au montage » une semaine avant le début des travaux.
Toutes les personnes impliquées dans le projet se sont alors rassemblées pour discuter sur place de toutes les éventualités : chef de projet, ingénieurs, électro-techniciens, monteurs, responsables des commandes et bien entendu le chef de poste et les représentants de la société fournissant la grue. La mise en service réussie du système de dépoussiérage à la fin d’un week-end de travail bien rempli a prouvé la pertinence du processus.
Pour la prochaine étape
En plus de la réduction des émissions, du niveau sonore et des besoins en énergie, le nouveau système de dépoussiérage offre notamment des avantages grâce à des réserves sous pression et à sa sécurité de fonctionnement.
De plus, le système est équipé de manches de filtres Ammatex afin d’offrir une longue durée de vie. Ces machines de filtres résistent aux températures élevées et sont imprégnés de PTFE par défaut. Même les coutures sont en PTFE. Le polytétrafluoroéthylène est communément appelé « téflon », pour les tissus on utilise le terme de « Gore-Tex ».
Les manches de filtres rendent inutile l’utilisation de clapets d’air frais. Aucun air supplémentaire n’est requis pour le nettoyage des toiles. La stabilité de la forme des manches de filtres est assurée par thermofixation. L'installation de dépoussiérage de Pleinfeld de type AFA 3089 offre une puissance de 63’000 Nm./h et est régulée par un convertisseur de fréquence.
La surface de filtre est de 1045 m2. C’est largement suffisant pour répondre aux exigences environnementales du fonctionnement du poste d’enrobage.
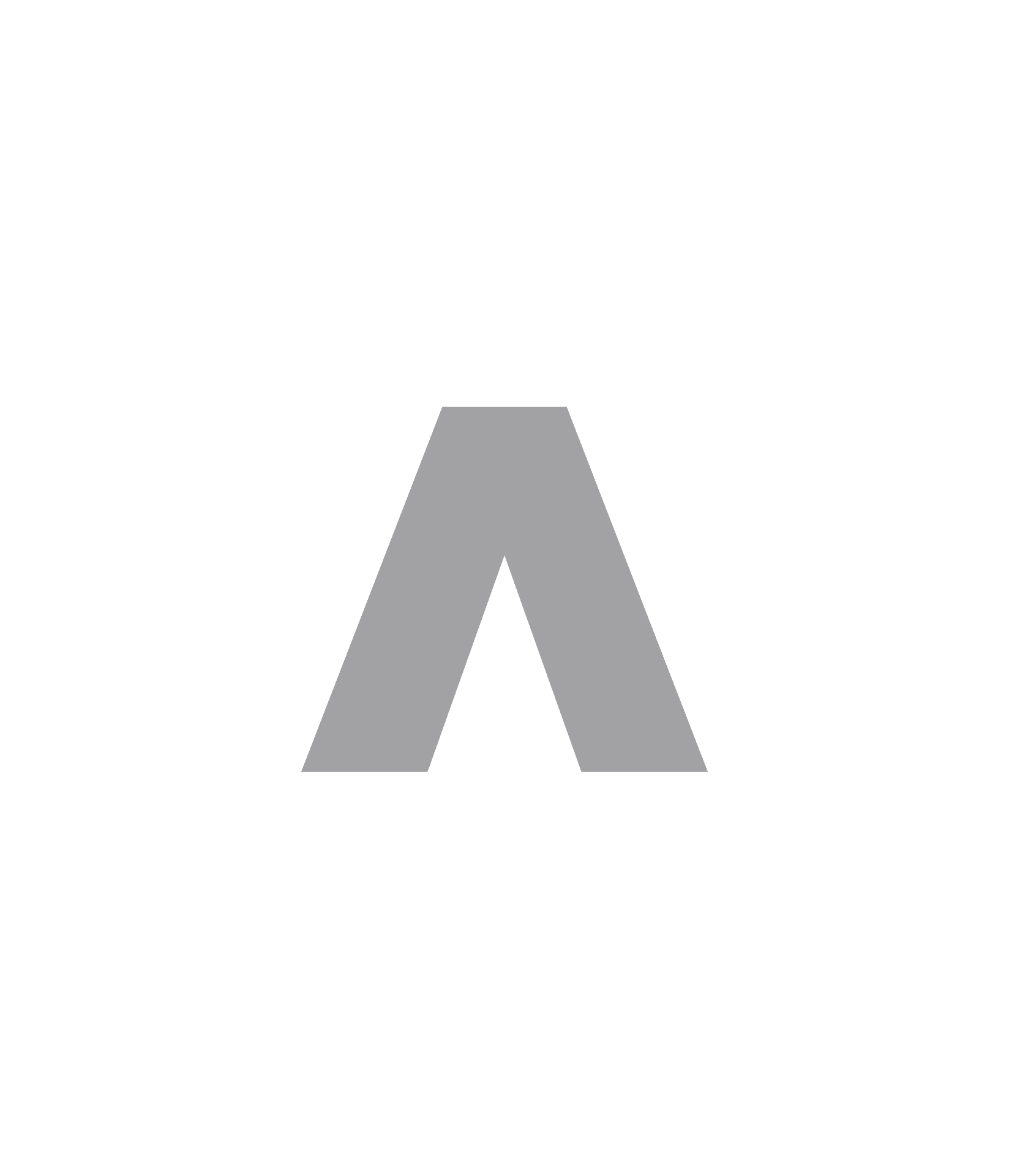
Formulaire de contact
Planifier une réunion en ligne
Prenez contact avec nous pour rencontrer un représentant commercial près de chez vous
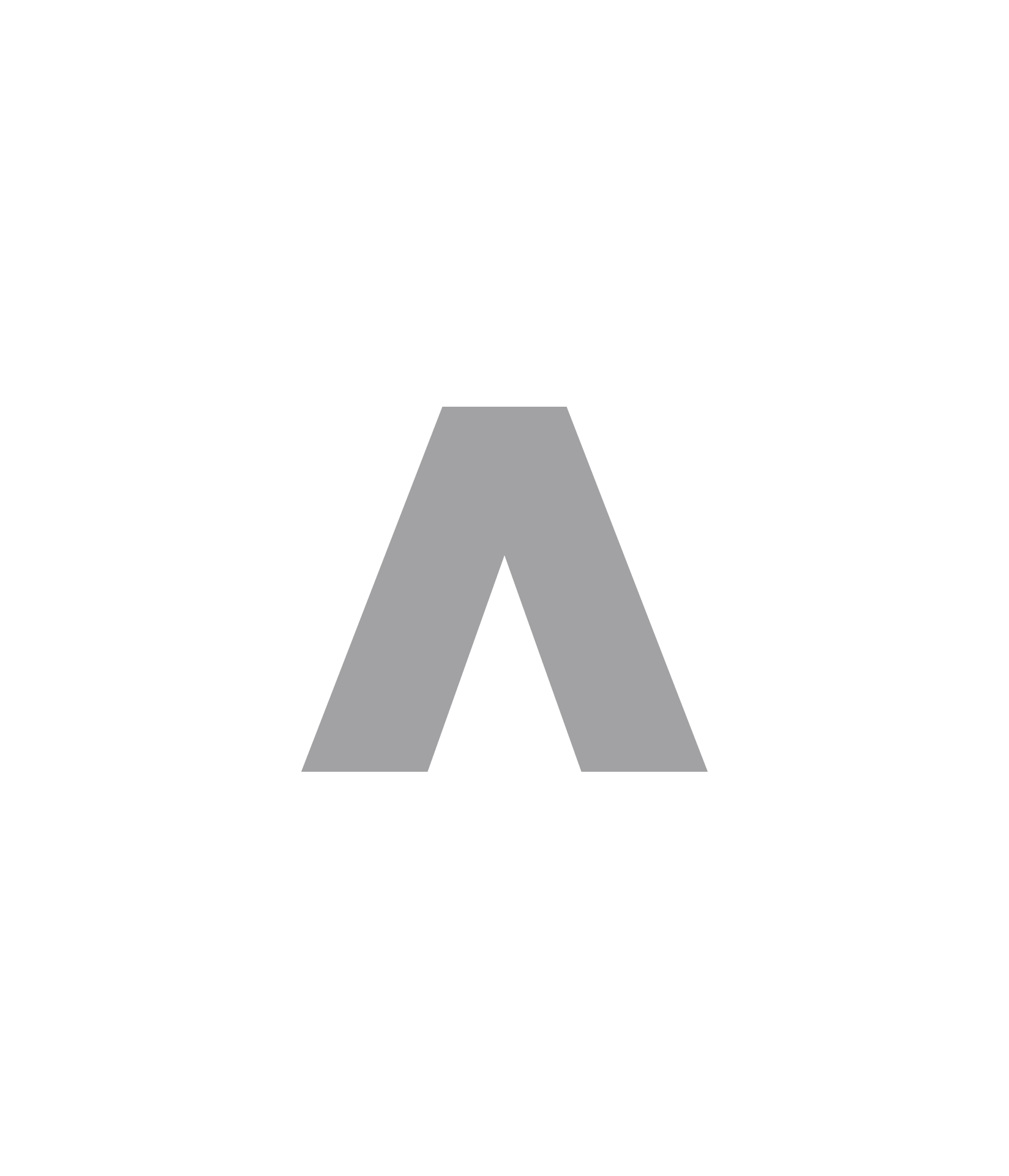