Hans-Christian Schneider
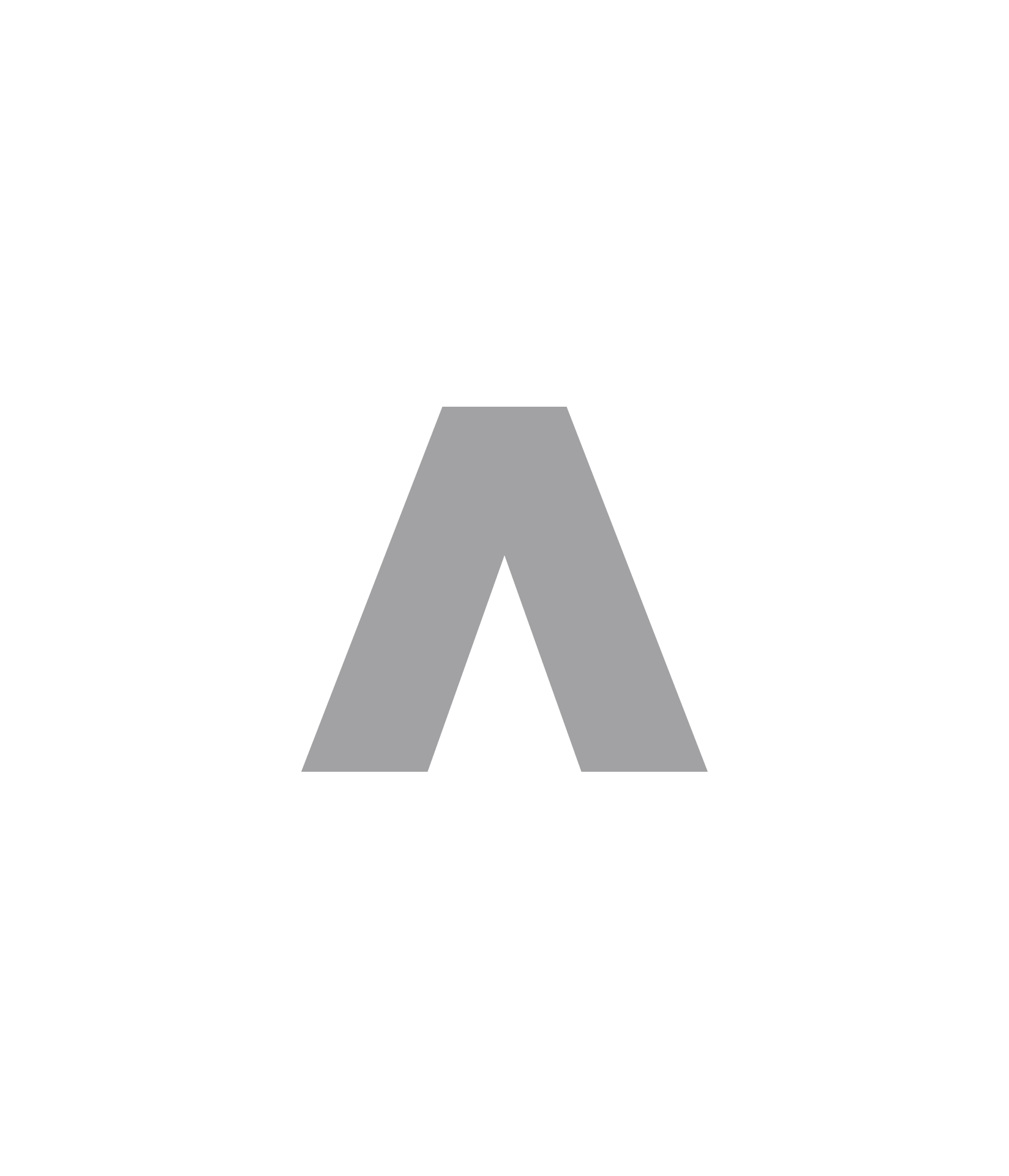
Hans-Christian est devenu CEO adjoint en janvier 2012, puis CEO en janvier 2013. Sa direction a déjà été marquée par une croissance significative et une présence internationale renforcée.
Trois fusions et acquisitions importantes ont eu lieu pendant ses deux premières années au poste de CEO : l’ouverture d’une usine de fabrication à Gravatai, au Brésil, la participation à une co-entreprise avec Apollo à Ahmedabad, en Inde, et l’acquisition d’Elba-Werk à Ettlingen, en Allemagne.
Ces décisions ont déjà profité à Ammann et montrent qu’un autre leader de la famille est prêt à saisir les opportunités pour garantir la réussite de l’entreprise.