Postes d’enrobage
L’AVIS DES CLIENTS CONTRIBUE AU DÉVELOPPEMENT D’UN NOUVEAU POSTE
COMMUNIQUÉ DE PRESSE DU GROUPE AMMANN
QUEENSLAND, Australie – Pendant de nombreuses années, l’investissement dans la production régionale d’asphalte a été négligé en raison des capitaux élevés requis pour établir une installation par rapport au retour sur investissement de la quantité limitée produite dans le secteur.
Cela oblige un producteur de la région à remplacer son installation par une solution à bas prix, souvent un poste mobile d’occasion ou un nouveau poste doté uniquement des fonctions de base et d’une technologie ancienne. Malheureusement, cette approche peut entraîner des compromis quant aux systèmes de sécurité, coûts de fonctionnement, longévité de la machine et qualité du mélange. Combiné à un accès limité aux pièces détachées et aux services de commande et d’entretien, tout ceci entraîne un résultat loin d’être optimal.
Sur certains chantiers relatifs au projet, il existe des problèmes lors du déplacement des postes mobiles dans le pays. Les réglementations et autorisations varient d’un Etat à l’autre, entraînant des délais et des complications lors du passage de frontières. De plus, les ADR (Australian Design Rules) sont plus restrictives pour les charges à l’essieu des remorques que celles d’autres pays, notamment en Europe et aux États-Unis. Pour la plupart des fabricants, cela implique des essieux supplémentaires et la formulation d’une conception spécifique à l’Australie, ce qui augmente le coût d’achat des postes.
En 2013, Dante Cremasco, Directeur général de l’infrastructure routière du groupe Downer, a demandé à Ammann d’étudier les marchés locaux. L’objectif était de parler aux opérateurs et équipes de production locales pour rassembler tous leurs souhaits et besoins afin de bien comprendre les restrictions, obstacles et blocages liés à leurs activités.
Dans le cadre de ce projet, Downer était un partenaire à part entière. En effet, en tant que leader de l’infrastructure routière et des services ferroviaires et miniers, il exploite plus de 35 postes d’enrobage en Australie. Downer est aussi une entreprise ouverte à la technologie, qui apporte constamment de nouvelles idées à Ammann afin d’élaborer de nouvelles solutions qui améliorent la branche.
Dante Cremasco a été le premier à commenter le projet. « En tant que producteur sur ces marchés régionaux, nous connaissons de nombreux pics et creux de production. Parallèlement, nous avons besoin d’une grande flexibilité pour produire tous les types de mélanges, y compris un pourcentage élevé de mélange à froid », explique-t-il. « Nous devons intégrer les nouveautés technologiques comme le recyclage, le mélange à chaud, l’utilisation de toners et d’oxydes aux zones régionales de projet, tout en réduisant l’empreinte carbone, l’investissement en capitaux, les coûts civils et de transport et logistique. »
Une fois cette visite réalisée par Ammann et les besoins réels des marchés déterminés, l’objectif a été défini et résumé ainsi :
Développer un poste modulable construit en Europe, équipé de la dernière technologie, concentré sur l’efficacité énergétique et les pertes minimes voire inexistantes, conforme aux normes australiennes dans tous les aspects et dimensionné pour un transport simple à l’aide des camions australiens standard (plates-formes et remorques), tout en conservant un prix compétitif par rapport aux postes fabriqués en Asie.
Paul Vandersluis, Directeur général d’Ammann Australie, s’est impliqué dans le projet dès le départ.
« En étroite collaboration avec les clients australiens, l’équipe Ammann locale et les concepteurs d’Ammann Allemagne, nous avons pu incorporer tout notre savoir-faire et notre expérience locaux des conditions de fonctionnement australiennes, avec la priorité australienne donnée à l’objectif zéro blessure, à la réduction des coûts de maintenance, à l’ergonomie, à l’élimination des pertes de production (démarrage/arrêt du poste) puis les associer à la technologie européenne la plus récente », explique Paul Vandersluis.
« Aucune piste n’a été négligée dans ce projet, chaque détail a été examiné d’un point de vue pratique pour simplifier la vie de l’opérateur. Ce projet a été très lourd en R&D, mais le résultat positif est déterminant pour le marché et comblera le vide que les marchés régionaux de projet attendaient avec impatience. »
Ce travail de R&D et design a donné naissance au nouveau poste Ammann ACT 140 ContiQuick.
Pour répondre à la question la plus fréquente, quels sont les avantages d’ACT 140 ContiQuick par rapport aux autres postes ?
- Asphalte de grande qualité grâce au malaxeur continu à deux arbres
- Capacité à réaliser de petites productions sans pertes
- Installation rapide avec coûts civils souterrains minimes
- Conforme à la norme australienne
- Dernières technologies pour produire un mélange à chaud, à froid et tiède et utiliser le recyclage
- Flexibilité pour produire de l’asphalte avec différents additifs
- Système de commande Ammann as1, leader à l’échelle internationale, incluant les dernières options comme Eco-view et Auto Loadout.
- Fabrication 100 % européenne
- Investissement estimé viable pour les marchés régionaux
- Transport et production sans compromis
L’approche dynamique d’Ammann dans la formulation de cette conception prouve que la meilleure façon de se développer et d’innover est de travailler en étroite collaboration avec les clients et de répondre à leurs besoins actuels et futurs. Selon la devise d’Ammann « Productivity Partnership for a Lifetime », le nouveau poste ACT 140 ContiQuick souligne une nouvelle fois l’engagement d’Ammann en faveur de la branche.
AMMANN EN BREF
Ammann est une entreprise familiale depuis six générations qui fabrique des postes d’enrobage et des centrales à béton ainsi que des machines de compactage et des finisseurs sur neuf sites de production situés en Europe, en Chine, en Inde et au Brésil. Son cœur de compétence est la construction de routes et les infrastructures de transport.

Formulaire de contact
Planifier une réunion en ligne
Prenez contact avec nous pour rencontrer un représentant commercial près de chez vous
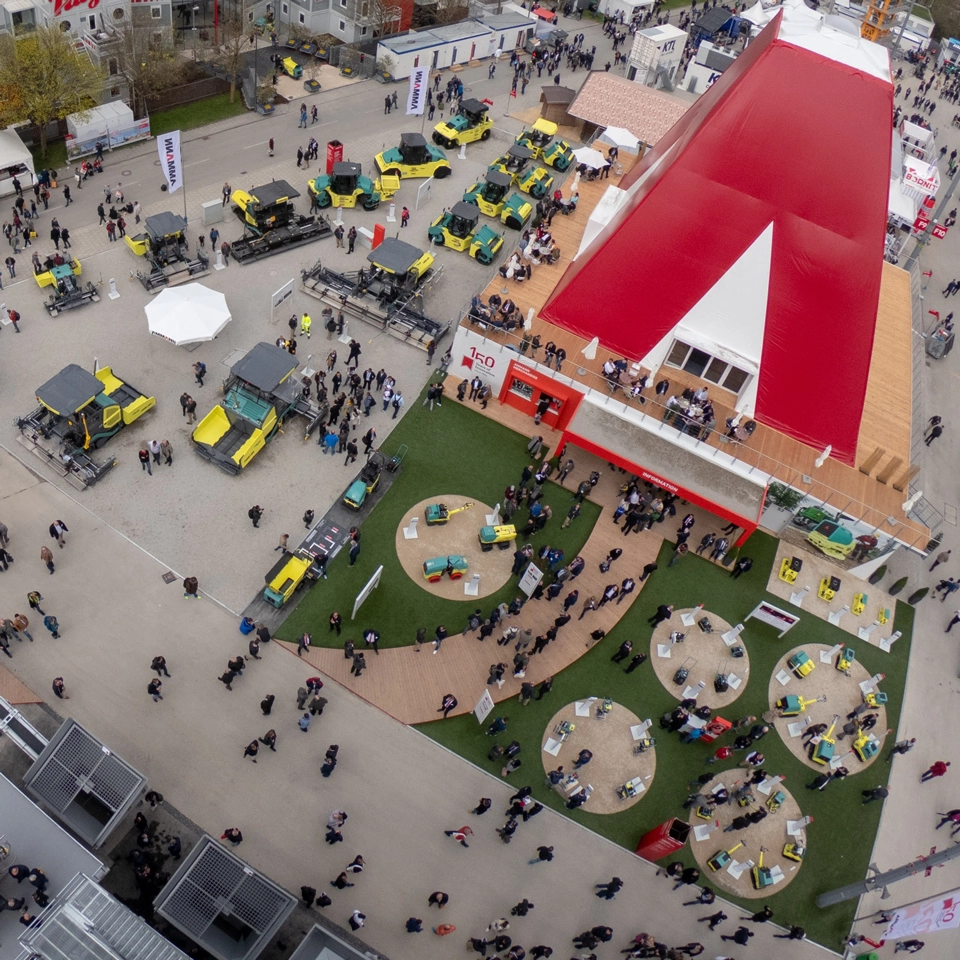