Plantas asfalticas
Una planta provee a dos aeropuertos
El contratista cumple plazos exigentes
La construcción de un aeropuerto es uno de los proyectos más estresantes que una empresa puede enfrentar. Los plazos son extremadamente rígidos y se ejecutan de manera estricta. La seguridad crea desafíos logísticos. Otras dificultades potenciales, como el clima, también pueden generar problemas.
La empresa de construcción griega Intrakat agregó una carga significativa a este escenario ya estresante: se hizo cargo de dos proyectos aeroportuarios con cronogramas muy próximos, con una sola planta para suministrar el asfalto. Intrakat utilizó la planta de mezcla de asfalto QuickBatch Ammann ABT optimizada para el transporte para producir mezclas en el aeropuerto de Mykonos en Grecia. Luego, la planta se comprimió y transportó a Kos, a más de 250 km de distancia, donde generó una mezcla para el proyecto del aeropuerto.
Usar la única planta suponía un importante ahorro de costos, pero también significaba que un plazo que no se cumpliera en el primer lugar de trabajo casi condenaría al segundo.
"Los márgenes de tiempo disponibles para ejecutar las obras en los aeropuertos de Mykonos y Kos fueron particularmente ajustados", dijo Panagiotis Anagnostopoulos, gerente de proyectos de Intrakat. “Si no hubiera sido posible mover la planta en el tiempo disponible, hubiéramos tenido que instalar dos plantas simultáneamente en ambos aeropuertos”.
14 aeropuertos en siete meses
Las pistas mejoradas en Mykonos y Kos son dos de los 14 aeropuertos griegos que se están revitalizando en un período de siete meses.
"Renovar y mejorar 14 aeropuertos en una de las regiones turísticas más populares del mundo, incluso durante la temporada baja, es un desafío y ahora tenemos por delante un período de reacondicionamiento y modernización de estos aeropuertos", dijo Rolf Klitscher, director de proyecto de Fraport Grecia, la concesionaria responsable del mantenimiento, la operación, la administración, la actualización y el desarrollo de los 14 aeropuertos regionales en Grecia durante los próximos 40 años. "Cuando realizamos un reacondicionamiento, tenemos muy poco tiempo, solo 20 días, para cerrar la pista".
Intrakat está manejando la producción de mezcla en los 14 aeropuertos y se toma el trabajo con mucha seriedad. "Uno de los proyectos de infraestructura más importantes que Intrakat ha emprendido es la mejora de los 14 aeropuertos regionales y sus expansiones por parte de Fraport Grecia", dijo Christos Papakatsikas, director de Airside en Intrakat.
El trabajo en Mykonos y Kos fue significativo e involucró el reemplazo completo del asfalto en ambos aeropuertos. "El volumen de las obras involucró unas 40 000 toneladas de mezclas de asfalto en Mykonos y 45 000 toneladas en Kos", dijo Papakatsikas.
¿Cómo cumplió Intrakat los exigentes plazos y finalizó ambos proyectos a tiempo?
PASO 1: Llegar rápido
QuickBatch ABT se basa en el concepto de logística del "principio de contenedor".
Los componentes clave, incluso las unidades del filtro y la secadora y los módulos de la torre de mezclado, se encuentran en carcasas que también sirven como contenedores de transporte certificados. Estos componentes están construidos en unidades de 20 o 40 pies, el tamaño de contenedor más común. Cuando sea el momento de movilizar los componentes, solo es necesario cargarlos dentro del vehículo de transporte. La planta entera cabe en 10 unidades.
"Es una planta móvil en contenedores que se puede transportar fácilmente a bajo costo", afirmó Jannis Charalambidis, gerente comercial de SPANOS Group I.K.E., el distribuidor de Ammann para Grecia. “Se puede instalar en solo un par de días sin la necesidad de ningún cimiento”.
Hay otro beneficio para los contenedores: son más económicos de transportar y los métodos para enviarlos son más accesibles; existen factores que pueden generar ahorros de costos sustanciales, especialmente si una planta debe reubicarse con frecuencia.
PASO 2: Instalarse rápidamente, también
"El desafío de trasladar la planta de Mykonos a Kos fue que tuvimos un período de dos semanas", dijo Klitscher. “Durante este tiempo, la planta de asfalto tuvo que ser desarmada, enviada y rearmada, incluida la puesta en marcha”.
La instalación estimada de Anagnostopoulos puede completarse en 10 a 12 días y desarmarse en ocho a 10 días. “Para la instalación y el desarmado, utilizamos dos grúas, así como una pequeña grúa telescópica hidráulica, que, en realidad, no era necesaria”, dijo.
No se requiere ningún cimiento, lo que implica más ahorro de tiempo y dinero. Los componentes son "conectar y utilizar”, lo que permite un montaje rápido.
PASO 3: Reciclar en el sitio
El trabajo requería el uso de asfalto reciclado (RAP) molido en el aeropuerto. ABT QuickBatch es un reciclador capaz, e Intrakat dio otro paso para ahorrar tiempo al emplear Ammann RSS 120-M, una trituradora, con granulador primario, granulador secundario y criba, todo integrado en una sola máquina.
RSS 120-M utiliza tecnología patentada, diseñada específicamente para RAP, molido o en bloques, que permite una trituración moderada a bajas revoluciones. Esto minimiza los finos en el RAP, haciendo que la manipulación y la incorporación del material reciclado en la mezcla caliente sea lo más eficiente posible.
RSS 120-M es una máquina móvil lista para usar dentro de los 30 minutos de llegar al lugar de trabajo. Por lo tanto, la máquina cumplió por completo con las necesidades de Intrakat en términos de movilidad, tiempo de instalación, producción en el sitio y finos reducidos.
"Este asfalto tiene que ser procesado antes de ser utilizado en producción, y el móvil Ammann RSS 120-M es una excelente solución", indicó Charalambidis.
PASO 4: Maximizar la producción
La capacidad de producción de la planta durante las obras en Mykonos y Kos alcanzó hasta 150 toneladas por hora. "No se esperaba, por supuesto, alcanzar la capacidad nominal de producción debido al retraso de la adición de polímeros a la mezcla, lo que requirió un tiempo de mezcla adicional", dijo Anagnostopoulos. "Fue completamente satisfactorio y definitivamente superó las expectativas".
El rendimiento de la producción demostró ser aún más esencial debido a los retrasos ocasionados por la lluvia. "La planta QuickBatch fue altamente productiva y flexible", dijo Papakatsikas. “De esta forma, pudimos recuperar el tiempo perdido debido a la lluvia y las malas condiciones climáticas en el tiempo restante asignado, trabajando en turnos dobles y ampliando el rendimiento de la planta”.
"Logramos completar el proyecto dentro de los plazos, superando las demoras debido al mal tiempo", dijo Papakatsikas. Fue un final feliz para todos.
La construcción de un aeropuerto es uno de los proyectos más estresantes que una empresa puede enfrentar. Los plazos son extremadamente rígidos y se ejecutan de manera estricta. La seguridad crea desafíos logísticos. Otras dificultades potenciales, como el clima, también pueden generar problemas.
La empresa de construcción griega Intrakat agregó una carga significativa a este escenario ya estresante: se hizo cargo de dos proyectos aeroportuarios con cronogramas muy próximos, con una sola planta para suministrar el asfalto. Intrakat utilizó la planta de mezcla de asfalto QuickBatch Ammann ABT optimizada para el transporte para producir mezclas en el aeropuerto de Mykonos en Grecia. Luego, la planta se comprimió y transportó a Kos, a más de 250 km de distancia, donde generó una mezcla para el proyecto del aeropuerto.
Usar la única planta suponía un importante ahorro de costos, pero también significaba que un plazo que no se cumpliera en el primer lugar de trabajo casi condenaría al segundo.
"Los márgenes de tiempo disponibles para ejecutar las obras en los aeropuertos de Mykonos y Kos fueron particularmente ajustados", dijo Panagiotis Anagnostopoulos, gerente de proyectos de Intrakat. “Si no hubiera sido posible mover la planta en el tiempo disponible, hubiéramos tenido que instalar dos plantas simultáneamente en ambos aeropuertos”.
14 aeropuertos en siete meses
Las pistas mejoradas en Mykonos y Kos son dos de los 14 aeropuertos griegos que se están revitalizando en un período de siete meses.
"Renovar y mejorar 14 aeropuertos en una de las regiones turísticas más populares del mundo, incluso durante la temporada baja, es un desafío y ahora tenemos por delante un período de reacondicionamiento y modernización de estos aeropuertos", dijo Rolf Klitscher, director de proyecto de Fraport Grecia, la concesionaria responsable del mantenimiento, la operación, la administración, la actualización y el desarrollo de los 14 aeropuertos regionales en Grecia durante los próximos 40 años. "Cuando realizamos un reacondicionamiento, tenemos muy poco tiempo, solo 20 días, para cerrar la pista".
Intrakat está manejando la producción de mezcla en los 14 aeropuertos y se toma el trabajo con mucha seriedad. "Uno de los proyectos de infraestructura más importantes que Intrakat ha emprendido es la mejora de los 14 aeropuertos regionales y sus expansiones por parte de Fraport Grecia", dijo Christos Papakatsikas, director de Airside en Intrakat.
El trabajo en Mykonos y Kos fue significativo e involucró el reemplazo completo del asfalto en ambos aeropuertos. "El volumen de las obras involucró unas 40 000 toneladas de mezclas de asfalto en Mykonos y 45 000 toneladas en Kos", dijo Papakatsikas.
¿Cómo cumplió Intrakat los exigentes plazos y finalizó ambos proyectos a tiempo?
PASO 1: Llegar rápido
QuickBatch ABT se basa en el concepto de logística del "principio de contenedor".
Los componentes clave, incluso las unidades del filtro y la secadora y los módulos de la torre de mezclado, se encuentran en carcasas que también sirven como contenedores de transporte certificados. Estos componentes están construidos en unidades de 20 o 40 pies, el tamaño de contenedor más común. Cuando sea el momento de movilizar los componentes, solo es necesario cargarlos dentro del vehículo de transporte. La planta entera cabe en 10 unidades.
"Es una planta móvil en contenedores que se puede transportar fácilmente a bajo costo", afirmó Jannis Charalambidis, gerente comercial de SPANOS Group I.K.E., el distribuidor de Ammann para Grecia. “Se puede instalar en solo un par de días sin la necesidad de ningún cimiento”.
Hay otro beneficio para los contenedores: son más económicos de transportar y los métodos para enviarlos son más accesibles; existen factores que pueden generar ahorros de costos sustanciales, especialmente si una planta debe reubicarse con frecuencia.
PASO 2: Instalarse rápidamente, también
"El desafío de trasladar la planta de Mykonos a Kos fue que tuvimos un período de dos semanas", dijo Klitscher. “Durante este tiempo, la planta de asfalto tuvo que ser desarmada, enviada y rearmada, incluida la puesta en marcha”.
La instalación estimada de Anagnostopoulos puede completarse en 10 a 12 días y desarmarse en ocho a 10 días. “Para la instalación y el desarmado, utilizamos dos grúas, así como una pequeña grúa telescópica hidráulica, que, en realidad, no era necesaria”, dijo.
No se requiere ningún cimiento, lo que implica más ahorro de tiempo y dinero. Los componentes son "conectar y utilizar”, lo que permite un montaje rápido.
PASO 3: Reciclar en el sitio
El trabajo requería el uso de asfalto reciclado (RAP) molido en el aeropuerto. ABT QuickBatch es un reciclador capaz, e Intrakat dio otro paso para ahorrar tiempo al emplear Ammann RSS 120-M, una trituradora, con granulador primario, granulador secundario y criba, todo integrado en una sola máquina.
RSS 120-M utiliza tecnología patentada, diseñada específicamente para RAP, molido o en bloques, que permite una trituración moderada a bajas revoluciones. Esto minimiza los finos en el RAP, haciendo que la manipulación y la incorporación del material reciclado en la mezcla caliente sea lo más eficiente posible.
RSS 120-M es una máquina móvil lista para usar dentro de los 30 minutos de llegar al lugar de trabajo. Por lo tanto, la máquina cumplió por completo con las necesidades de Intrakat en términos de movilidad, tiempo de instalación, producción en el sitio y finos reducidos.
"Este asfalto tiene que ser procesado antes de ser utilizado en producción, y el móvil Ammann RSS 120-M es una excelente solución", indicó Charalambidis.
PASO 4: Maximizar la producción
La capacidad de producción de la planta durante las obras en Mykonos y Kos alcanzó hasta 150 toneladas por hora. "No se esperaba, por supuesto, alcanzar la capacidad nominal de producción debido al retraso de la adición de polímeros a la mezcla, lo que requirió un tiempo de mezcla adicional", dijo Anagnostopoulos. "Fue completamente satisfactorio y definitivamente superó las expectativas".
El rendimiento de la producción demostró ser aún más esencial debido a los retrasos ocasionados por la lluvia. "La planta QuickBatch fue altamente productiva y flexible", dijo Papakatsikas. “De esta forma, pudimos recuperar el tiempo perdido debido a la lluvia y las malas condiciones climáticas en el tiempo restante asignado, trabajando en turnos dobles y ampliando el rendimiento de la planta”.
"Logramos completar el proyecto dentro de los plazos, superando las demoras debido al mal tiempo", dijo Papakatsikas. Fue un final feliz para todos.
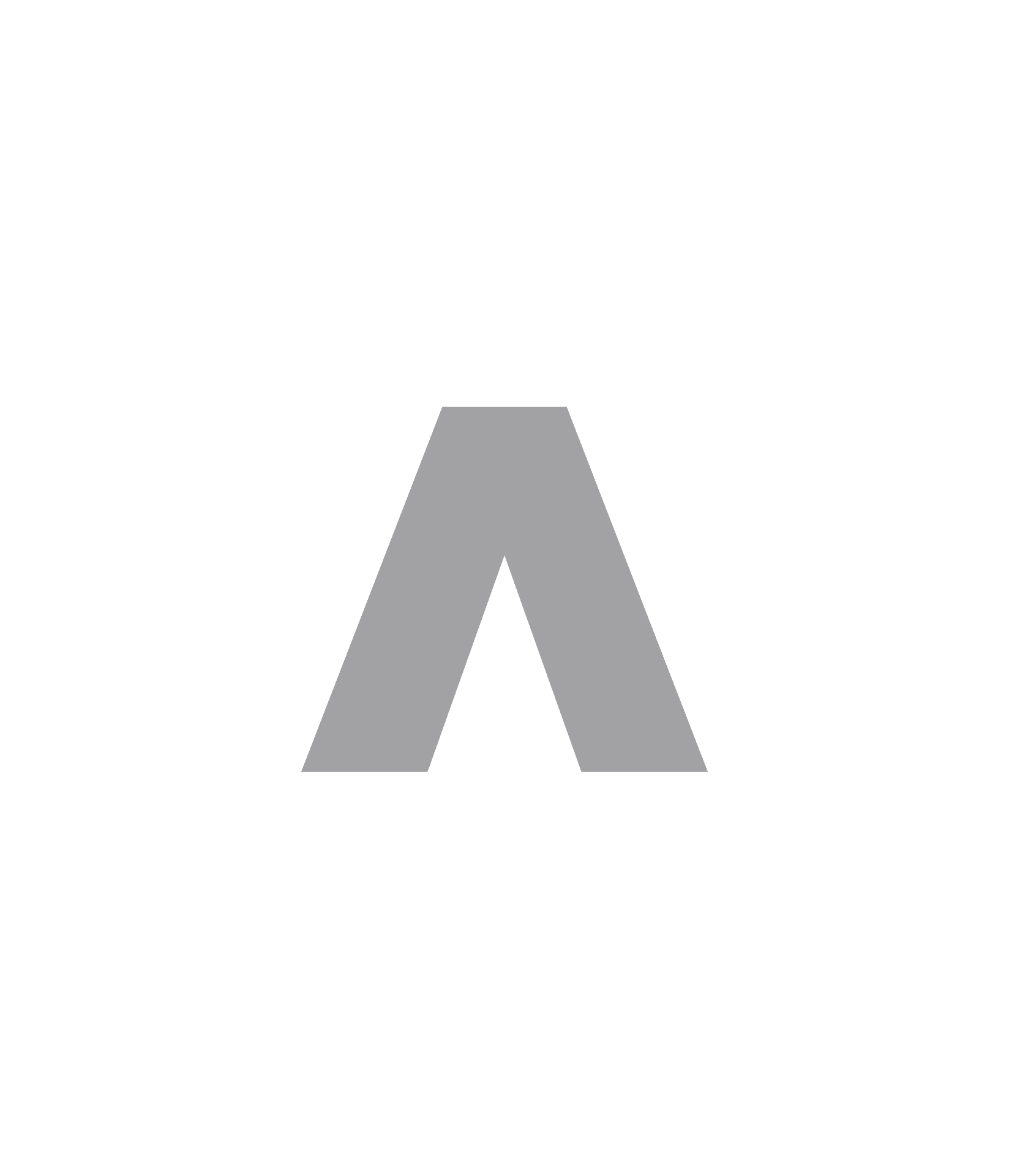
Formulario de contacto
Programe una reunión en línea
Póngase en contacto con nosotros para conocer a un representante de ventas cerca de usted
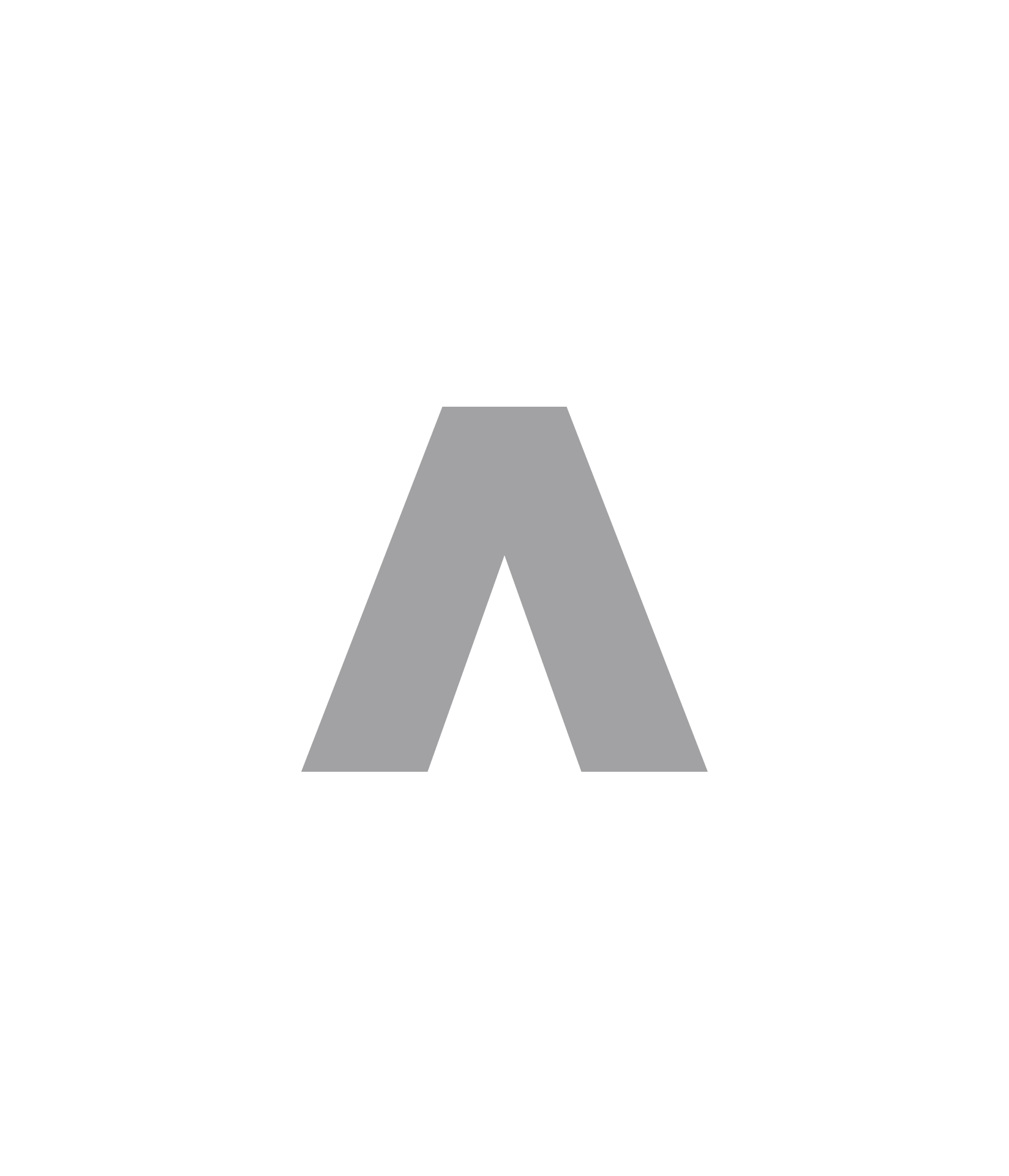