Postes d’enrobage
Un poste Ammann fournit de l’enrobé pour deux aéroports en Grèce
Un poste Ammann fournit de l’enrobé pour deux aéroports en Grèce
Pour une entreprise, la construction d’un aéroport fait partie des projets les plus stressants. Les délais sont extrêmement rigides et sont appliqués de manière stricte. La sécurité est également une source de défis logistiques. D’autres écueils, comme la météo, peuvent également être source de contraintes.
La société de construction grecque Intrakat a ajouté un incommodité significatif à ce scénario déjà stressant : elle a pris en charge deux projets d’aéroport au planning très serré, avec un seul poste pour fournir l’enrobé. Intrakat a utilisé le poste d’enrobage mobile Ammann ABT QuickBatch pour produire le mélange requis sur l’aéroport de Mykonos, en Grèce. Le poste fut ensuite démonté et transporté par ferry à Kos, à plus de 250 km, où il a produit le mélange pour un deuxième aéroport.
L’utilisation d’un seul poste permettait de réaliser d’importantes économies sur les coûts, mais tout retard sur le premier chantier aurait également mis en péril le second.
«Les délais pour l’exécution des travaux sur les aéroports de Mykonos et de Kos étaient particulièrement étroits», explique Panagiotis Anagnostopoulos, chef de projet chez Intrakat. «S’il n’avait pas été possible de déplacer le poste d’enrobage dans le temps impartis, nous aurions dû installer deux postes simultanément sur les deux aéroports.»
14 aéroports en sept mois
La restauration des pistes de Mykonos et de Kos faisant partis d’un projet de restauration de 14 aéroports grecs réhabilités au cours d’une période de sept mois.
«Intervenir sur 14 aéroports dans l’une des régions les plus touristiques au monde, même pendant la basse saison, est un véritable défi. », déclare Rolf Klitscher, directeur des projets chez Fraport Grèce, le concessionnaire responsable de la maintenance, de l’exploitation, de la gestion, de la restauration et du développement des 14 aéroports régionaux de Grèce au cours des 40 prochaines années. «Lorsque nous nous chargeons d’une restauration, nous avons très peu de temps, seulement 20 jours, pour fermer la piste.»
Intrakat se charge de la production du mélange sur les 14 aéroports et prend sa tâche très au sérieux. «L’un des plus importants projets d’infrastructure menés par Intrakat consiste en la restauration des 14 aéroports régionaux et en leur développement par Fraport Grèce», ajoute Christos Papakatsikas, Directeur Aéronautique chez Intrakat.
Le travail mené à Mykonos et Kos était exigeant, impliquant le remplacement complet de l’enrobé des deux aéroports. «Le volume des travaux impliquait environ 40 000 tonnes d’enrobé à Mykonos et 45 000 tonnes à Kos», explique Christos Papakatsikas.
Comment Intrakat a-t-elle réussi à respecter les délais exigeants et à finir les deux projets dans les temps?
ETAPE 1 : Se déplacer rapidement
L’ABT QuickBatch est conçu selon le principe logistique de type «conteneur».
Les principaux composants au cœur du système, dont les unités de filtrage/séchage et les modules malaxeurs, se trouvent dans des carters qui servent également de conteneurs de transport. Les composants sont fabriqués sous la forme d’unités de 20 ou 40 pieds, qui sont les tailles de conteneur les plus communes. Lorsqu’il est nécessaire de déplacer le poste d’enrobage, les composants sont simplement chargés sur le véhicule de transport. L’ensemble du poste d’enrobage tient dans 10 unités.
«C’est un poste mobile type conteneurs qui se transporte facilement pour un coût réduit», déclare Jannis Charalambidis, responsable commercial chez SPANOS Group I.K.E., le revendeur Ammann en Grèce. «Il s’installe en quelques jours sans nécessiter de fondation.»
Les conteneurs ont un autre avantage : ils réduisent les coûts de transport et les méthodes d’expédition sont familières. Ce sont des facteurs susceptibles de permettre une réduction substantielle des coûts, en particulier lorsqu’un poste d’enrobage doit être souvent déplacé.
ETAPE 2 : Installer l’équipement rapidement
«Le défi posé par le déplacement du poste d’enrobage de Mykonos à Kos était que nous avions une contrainte de temps de deux semaines», ajoute M. Klitscher. «Au cours de cette période, le poste d’enrobage devait être démonté, expédié, remonté et remis en service.»
M. Anagnostopoulos estimait que l’installation pouvait être réalisée en 10 à 12 jours, et le démontage en 8 à 10 jours. «Pour l’installation et le démontage, nous avons utilisé deux grues ainsi qu’une petite grue télescopique hydraulique qui n’était en fait pas utile», déclare-t-il.
Le fait qu’aucune fondation ne soit requise permet également d’économiser du temps et de l’argent. Les composants suivent une approche «plug-and-play», ce qui assure un montage rapide.
ETAPE 3 : Recycler sur site
Le chantier nécessitait l’utilisation d’enrobé recyclé (RAP) broyé sur l’aéroport. L’ABT QuickBatch est un système permettant le recyclage et Intrakat a pris une autre mesure permettant de gagner du temps en utilisant le broyeur Ammann RSS 120-M qui intègre en une seule machine un granulateur primaire, un granulateur secondaire et un crible.
Le RSS 120-M utilise une technologie brevetée spécialement conçue pour le RAP, broyé ou en plaques, qui permet un concassage en douceur à faible vitesse. Cela réduit les fines dans le RAP, rendant la manipulation et l’incorporation du matériau recyclé dans le mélange chaud aussi efficaces que possible.
Le RSS 120-M est une machine mobile qui est prête à fonctionner en moins de 30 minutes après son arrivée sur le chantier. Elle répondait donc parfaitement aux besoins d’Intrakat en termes de mobilité, de temps d’installation, de production sur site et de réduction des fines.
«Cet enrobé doit être traité avant d’être utilisé en production, et l’Ammann RSS 120-M mobile est une excellente solution», déclare M. Charalambidis.
ETAPE 4 : Maximiser la production
Lors des travaux à Mykonos et à Kos, la capacité de production du poste a atteint jusqu’à 150 tonnes par heure. «Bien entendu, on ne s’attendait pas à atteindre la capacité de production nominale en raison du délai dû à l’ajout de polymères au mélange, ce qui nécessite un temps de malaxage plus long, explique M. Anagnostopoulos. C’était tout à fait satisfaisant et dépassait définitivement nos attentes.»
Le rendement de production s’est avéré être encore plus essentiel en raison de retards dus à la pluie. «Le poste d’enrobage QuickBatch était très productif et très flexible», déclare M. Papakatsikas. «Nous avons ainsi pu rattraper le temps perdu à cause de la pluie et du mauvais temps sans dépasser les délais, en travaillant à deux équipes et en exploitant au maximum les performances du poste.»
«Nous avons réussi à terminer le projet dans les temps, en surmontant les retards dus au mauvais temps», ajoute M. Papakatsikas. Ce fut une fin heureuse pour tous.
Pour une entreprise, la construction d’un aéroport fait partie des projets les plus stressants. Les délais sont extrêmement rigides et sont appliqués de manière stricte. La sécurité est également une source de défis logistiques. D’autres écueils, comme la météo, peuvent également être source de contraintes.
La société de construction grecque Intrakat a ajouté un incommodité significatif à ce scénario déjà stressant : elle a pris en charge deux projets d’aéroport au planning très serré, avec un seul poste pour fournir l’enrobé. Intrakat a utilisé le poste d’enrobage mobile Ammann ABT QuickBatch pour produire le mélange requis sur l’aéroport de Mykonos, en Grèce. Le poste fut ensuite démonté et transporté par ferry à Kos, à plus de 250 km, où il a produit le mélange pour un deuxième aéroport.
L’utilisation d’un seul poste permettait de réaliser d’importantes économies sur les coûts, mais tout retard sur le premier chantier aurait également mis en péril le second.
«Les délais pour l’exécution des travaux sur les aéroports de Mykonos et de Kos étaient particulièrement étroits», explique Panagiotis Anagnostopoulos, chef de projet chez Intrakat. «S’il n’avait pas été possible de déplacer le poste d’enrobage dans le temps impartis, nous aurions dû installer deux postes simultanément sur les deux aéroports.»
14 aéroports en sept mois
La restauration des pistes de Mykonos et de Kos faisant partis d’un projet de restauration de 14 aéroports grecs réhabilités au cours d’une période de sept mois.
«Intervenir sur 14 aéroports dans l’une des régions les plus touristiques au monde, même pendant la basse saison, est un véritable défi. », déclare Rolf Klitscher, directeur des projets chez Fraport Grèce, le concessionnaire responsable de la maintenance, de l’exploitation, de la gestion, de la restauration et du développement des 14 aéroports régionaux de Grèce au cours des 40 prochaines années. «Lorsque nous nous chargeons d’une restauration, nous avons très peu de temps, seulement 20 jours, pour fermer la piste.»
Intrakat se charge de la production du mélange sur les 14 aéroports et prend sa tâche très au sérieux. «L’un des plus importants projets d’infrastructure menés par Intrakat consiste en la restauration des 14 aéroports régionaux et en leur développement par Fraport Grèce», ajoute Christos Papakatsikas, Directeur Aéronautique chez Intrakat.
Le travail mené à Mykonos et Kos était exigeant, impliquant le remplacement complet de l’enrobé des deux aéroports. «Le volume des travaux impliquait environ 40 000 tonnes d’enrobé à Mykonos et 45 000 tonnes à Kos», explique Christos Papakatsikas.
Comment Intrakat a-t-elle réussi à respecter les délais exigeants et à finir les deux projets dans les temps?
ETAPE 1 : Se déplacer rapidement
L’ABT QuickBatch est conçu selon le principe logistique de type «conteneur».
Les principaux composants au cœur du système, dont les unités de filtrage/séchage et les modules malaxeurs, se trouvent dans des carters qui servent également de conteneurs de transport. Les composants sont fabriqués sous la forme d’unités de 20 ou 40 pieds, qui sont les tailles de conteneur les plus communes. Lorsqu’il est nécessaire de déplacer le poste d’enrobage, les composants sont simplement chargés sur le véhicule de transport. L’ensemble du poste d’enrobage tient dans 10 unités.
«C’est un poste mobile type conteneurs qui se transporte facilement pour un coût réduit», déclare Jannis Charalambidis, responsable commercial chez SPANOS Group I.K.E., le revendeur Ammann en Grèce. «Il s’installe en quelques jours sans nécessiter de fondation.»
Les conteneurs ont un autre avantage : ils réduisent les coûts de transport et les méthodes d’expédition sont familières. Ce sont des facteurs susceptibles de permettre une réduction substantielle des coûts, en particulier lorsqu’un poste d’enrobage doit être souvent déplacé.
ETAPE 2 : Installer l’équipement rapidement
«Le défi posé par le déplacement du poste d’enrobage de Mykonos à Kos était que nous avions une contrainte de temps de deux semaines», ajoute M. Klitscher. «Au cours de cette période, le poste d’enrobage devait être démonté, expédié, remonté et remis en service.»
M. Anagnostopoulos estimait que l’installation pouvait être réalisée en 10 à 12 jours, et le démontage en 8 à 10 jours. «Pour l’installation et le démontage, nous avons utilisé deux grues ainsi qu’une petite grue télescopique hydraulique qui n’était en fait pas utile», déclare-t-il.
Le fait qu’aucune fondation ne soit requise permet également d’économiser du temps et de l’argent. Les composants suivent une approche «plug-and-play», ce qui assure un montage rapide.
ETAPE 3 : Recycler sur site
Le chantier nécessitait l’utilisation d’enrobé recyclé (RAP) broyé sur l’aéroport. L’ABT QuickBatch est un système permettant le recyclage et Intrakat a pris une autre mesure permettant de gagner du temps en utilisant le broyeur Ammann RSS 120-M qui intègre en une seule machine un granulateur primaire, un granulateur secondaire et un crible.
Le RSS 120-M utilise une technologie brevetée spécialement conçue pour le RAP, broyé ou en plaques, qui permet un concassage en douceur à faible vitesse. Cela réduit les fines dans le RAP, rendant la manipulation et l’incorporation du matériau recyclé dans le mélange chaud aussi efficaces que possible.
Le RSS 120-M est une machine mobile qui est prête à fonctionner en moins de 30 minutes après son arrivée sur le chantier. Elle répondait donc parfaitement aux besoins d’Intrakat en termes de mobilité, de temps d’installation, de production sur site et de réduction des fines.
«Cet enrobé doit être traité avant d’être utilisé en production, et l’Ammann RSS 120-M mobile est une excellente solution», déclare M. Charalambidis.
ETAPE 4 : Maximiser la production
Lors des travaux à Mykonos et à Kos, la capacité de production du poste a atteint jusqu’à 150 tonnes par heure. «Bien entendu, on ne s’attendait pas à atteindre la capacité de production nominale en raison du délai dû à l’ajout de polymères au mélange, ce qui nécessite un temps de malaxage plus long, explique M. Anagnostopoulos. C’était tout à fait satisfaisant et dépassait définitivement nos attentes.»
Le rendement de production s’est avéré être encore plus essentiel en raison de retards dus à la pluie. «Le poste d’enrobage QuickBatch était très productif et très flexible», déclare M. Papakatsikas. «Nous avons ainsi pu rattraper le temps perdu à cause de la pluie et du mauvais temps sans dépasser les délais, en travaillant à deux équipes et en exploitant au maximum les performances du poste.»
«Nous avons réussi à terminer le projet dans les temps, en surmontant les retards dus au mauvais temps», ajoute M. Papakatsikas. Ce fut une fin heureuse pour tous.

Formulaire de contact
Planifier une réunion en ligne
Prenez contact avec nous pour rencontrer un représentant commercial près de chez vous
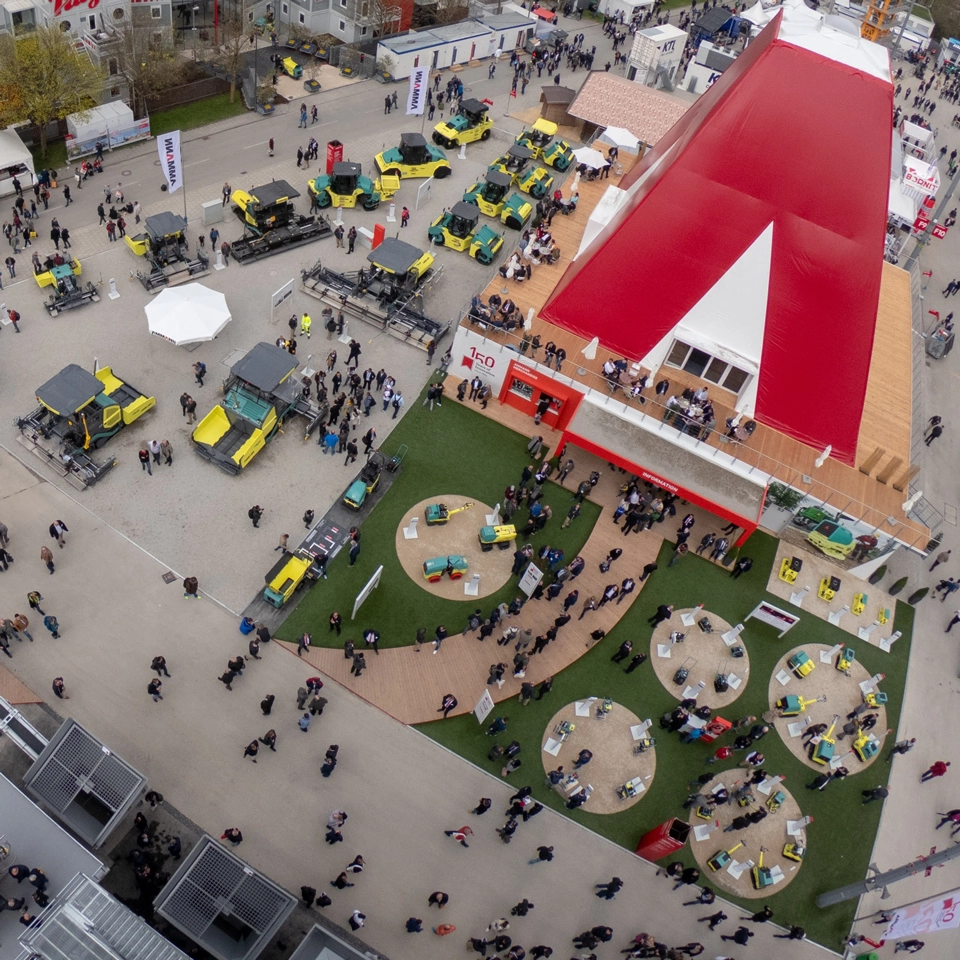