Hans-Christian Schneider
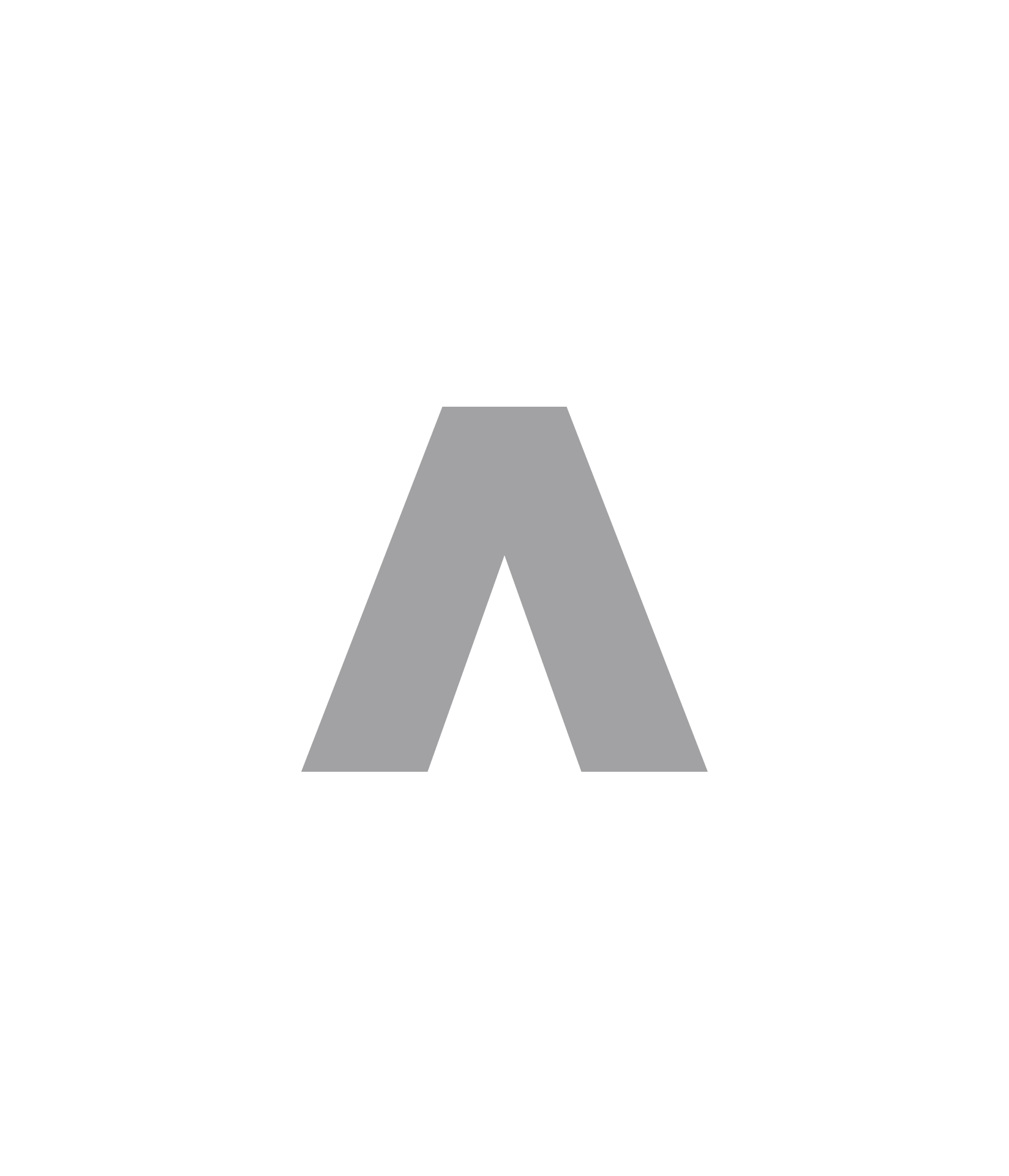
Hans-Christian became deputy CEO in January 2012 and CEO in January 2013. His tenure has already been marked by significant growth and an even stronger global presence.
Three significant mergers and acquisitions took place during his first two years as CEO: The opening of a manufacturing facility in Gravatai, Brazíl; entering a joint venture with Apollo in Ahmedabad, India; and the acquisition of Elba-Werk in Ettlingen, Germany.
The decisions already have benefitted Ammann and show yet another family leader is poised to seize opportunities to ensure the company’s continued success.