Concrete Plants
Silos Give Plant Expanded Life
Plant Adds Capacity, Maintains Mobility
BKG Transportbeton GmbH + Co. KG develops concrete for projects that include road building, but a year ago the company found itself at a crossroads of its own.
The business, near Karlsruhe, Germany, had found success with its Ammann Elba ESM 110 Concrete-Mixing Plant and its 4 80-tonne storage silos. The mobile plant had performed well since being purchased about 5 years ago and already had been moved successfully once.
Yet the market increasingly demanded more varied concretes. The ESM plant was able to meet those requests because of its built-in ability to create special products such as steel-fibre concrete, self-compacting concrete and paving concrete.
While the plant could handle the variety, the 4 storage units were not enough. Mr. Dieter Sülflow, Managing Director of BKG Transportbeton GmbH + Co. KG, saw a way to reach additional customers who needed the specialised concrete at a fraction of the cost of investing in a new plant.
BKG Transportbeton GmbH + Co. KG investigated the addition of 3 silos, each with a storage capacity of 80 tonnes. The solution was tricky because the plant was on a small site with little room for new equipment, let alone the addition of 3 silos.
“The biggest challenge was to integrate the new mobile silos into the existing plant configuration,” Sülflow said. The new silos also had to fit into the plant’s overall concept of mobility.
The company turned to Ammann Elba, which had proven to be a helpful partner during earlier work installing and relocating the plant. After-sales support also created confidence in Ammann Elba. “Specifically, the service staff of Ammann Elba left a positive impression,” Sülflow said.
Together a team from BKG and Ammann Elba determined the best locations and process to fully integrate the new silos into the production process. The result is a company that can develop more varied products while also improving production and availability of all concretes.
BKG Transportbeton GmbH + Co. KG develops concrete for projects that include road building, but a year ago the company found itself at a crossroads of its own.
The business, near Karlsruhe, Germany, had found success with its Ammann Elba ESM 110 Concrete-Mixing Plant and its 4 80-tonne storage silos. The mobile plant had performed well since being purchased about 5 years ago and already had been moved successfully once.
Yet the market increasingly demanded more varied concretes. The ESM plant was able to meet those requests because of its built-in ability to create special products such as steel-fibre concrete, self-compacting concrete and paving concrete.
While the plant could handle the variety, the 4 storage units were not enough. Mr. Dieter Sülflow, Managing Director of BKG Transportbeton GmbH + Co. KG, saw a way to reach additional customers who needed the specialised concrete at a fraction of the cost of investing in a new plant.
BKG Transportbeton GmbH + Co. KG investigated the addition of 3 silos, each with a storage capacity of 80 tonnes. The solution was tricky because the plant was on a small site with little room for new equipment, let alone the addition of 3 silos.
“The biggest challenge was to integrate the new mobile silos into the existing plant configuration,” Sülflow said. The new silos also had to fit into the plant’s overall concept of mobility.
The company turned to Ammann Elba, which had proven to be a helpful partner during earlier work installing and relocating the plant. After-sales support also created confidence in Ammann Elba. “Specifically, the service staff of Ammann Elba left a positive impression,” Sülflow said.
Together a team from BKG and Ammann Elba determined the best locations and process to fully integrate the new silos into the production process. The result is a company that can develop more varied products while also improving production and availability of all concretes.
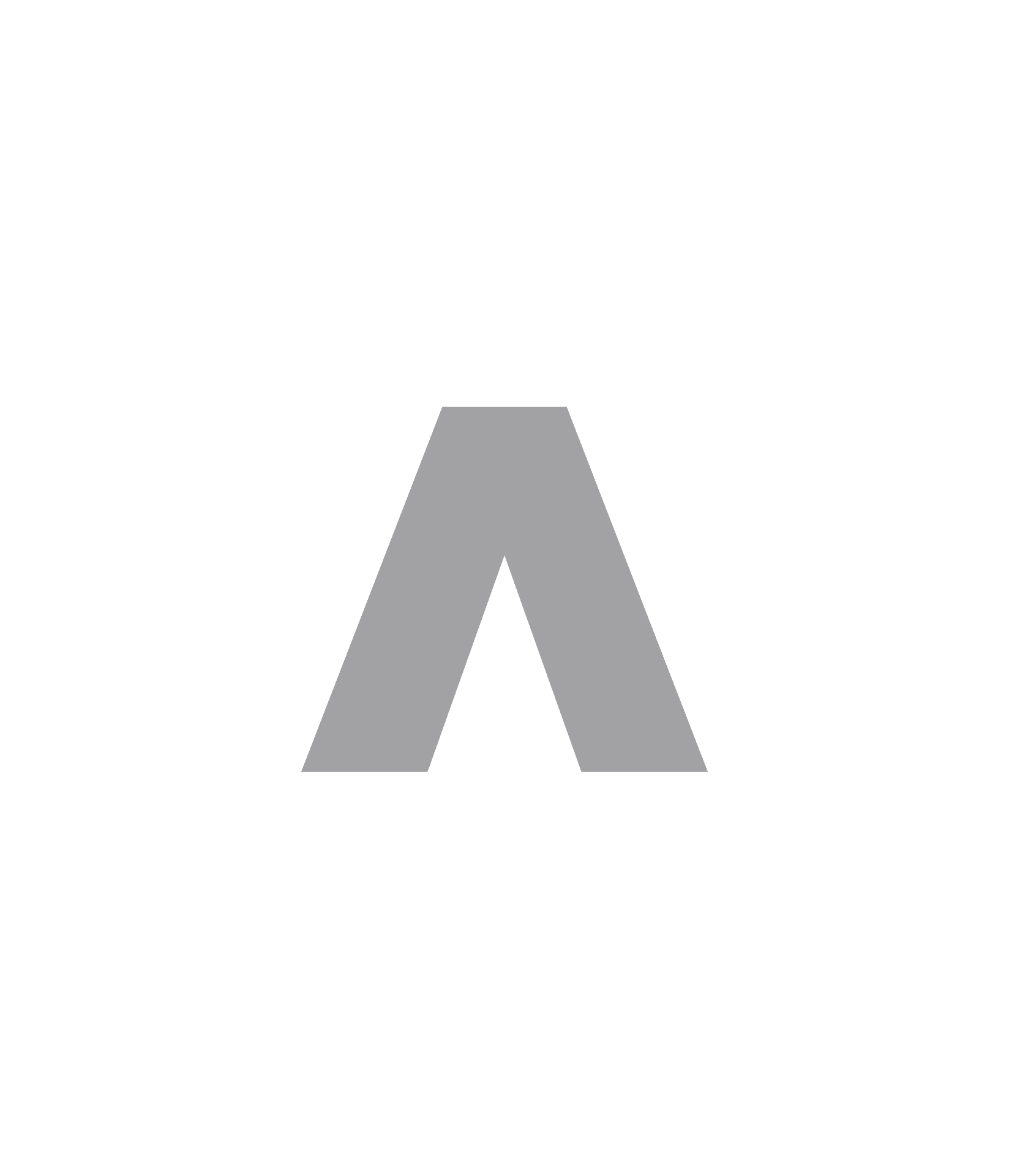
Contact Form
Schedule online meeting
Get in touch with us to meet a sales representative near you
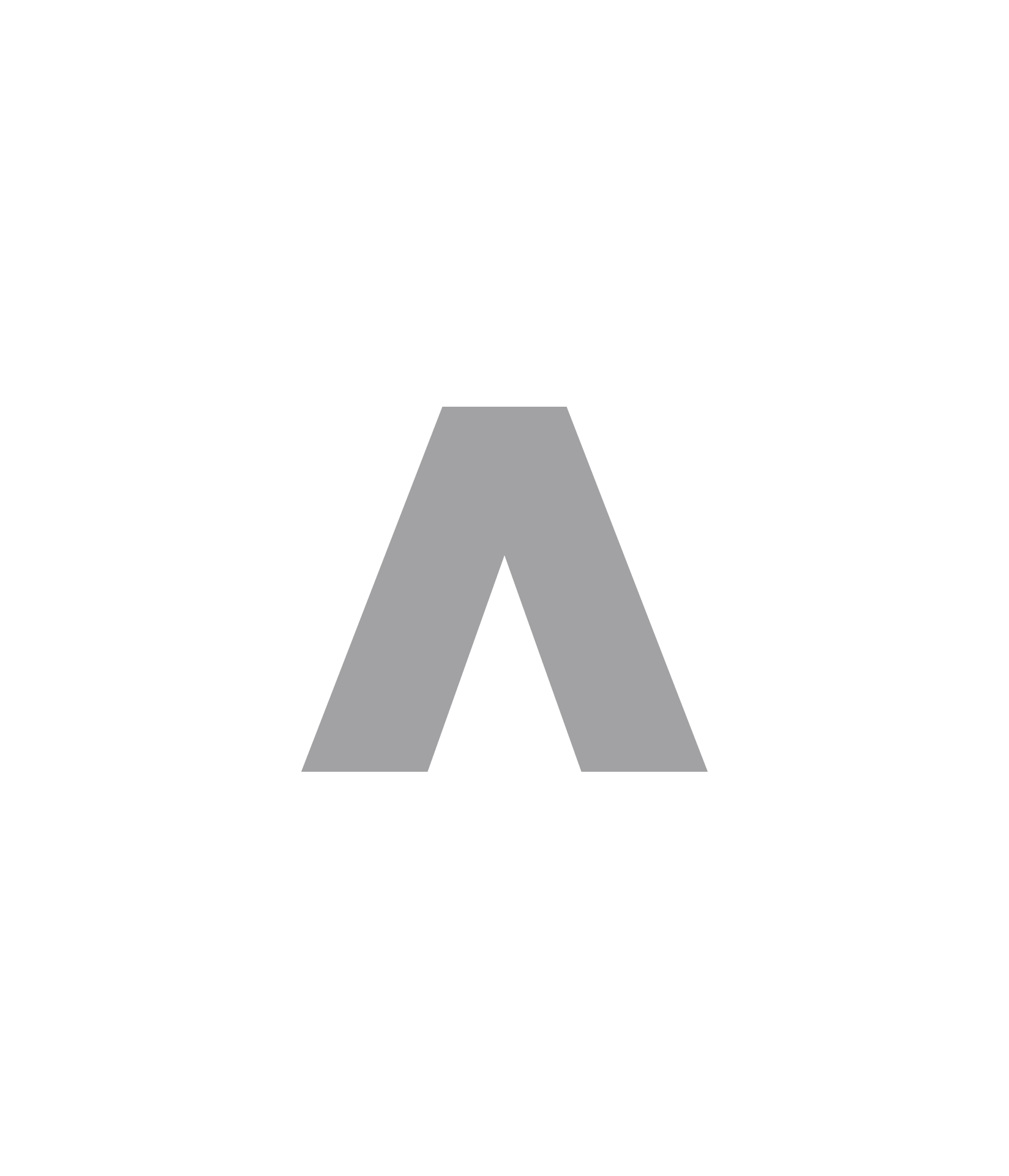