Energy efficiency and low emissions
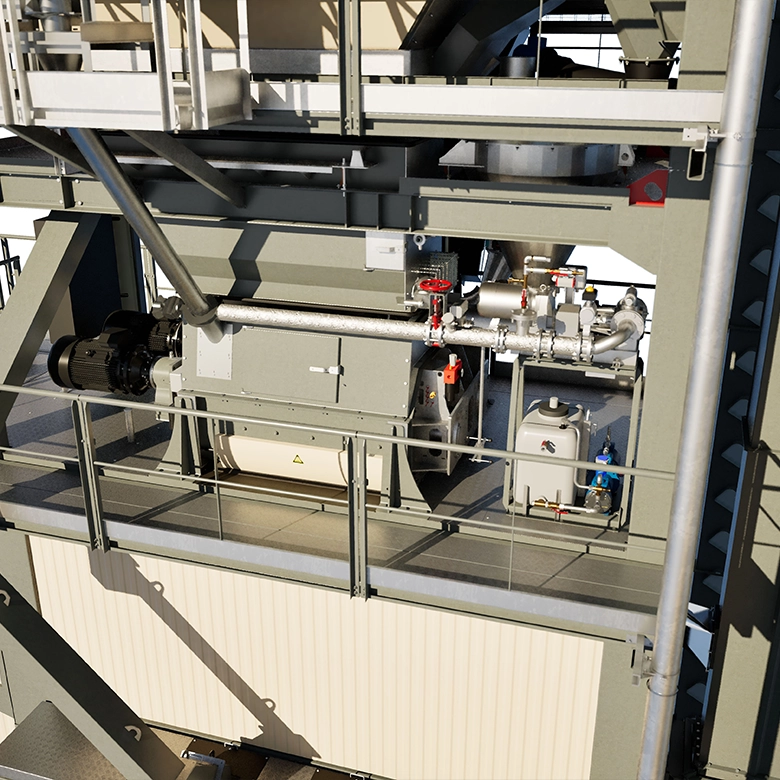
New technologies enable the manufacturing of asphalt at reduced temperatures. The energy consumption per tonne of asphalt and the emissions at the road construction site drop significantly. While conventional asphalt is produced at around 170°C, the low-temperature processes of today allow production temperatures of around 100°C. Ammann offers various technologies for this. Foam bitumen, waxes and other additives, special bitumen or alternative mixing cycles can be suitable for use, depending on the application.