Asphaltmischanlagen
Eine Anlage versorgt zwei Flughäfen
Bauunternehmen hält knappe Zeitvorgaben ein
Flughafenarbeiten gehören zu den heikelsten Projekten, die ein Bauunternehmen zu bewältigen hat. Die Termine sind extrem knapp bemessen und müssen strikt eingehalten werden. Die Sicherheitsvorkehrungen stellen eine logistische Herausforderung dar. Hinzu kommen andere Unwägbarkeiten wie das Wetter.
Das griechische Bauunternehmen Intrakat hat dieses heikle Szenario nochmals verschärft: Es hat zwei Flughafenprojekte mit eng beieinander liegenden Fertigstellungsterminen übernommen – mit nur einer Asphaltmischanlage. Für die Herstellung der Mischung für den Flughafen von Mykonos verwendete Intrakat die transportoptimierte ABT QuickBatch von Ammann. Danach wurde die Anlage verpackt und in das über 250 Kilometer entfernte Kos verfrachtet, wo sie das Mischgut für ein zweites Flughafenprojekt herstellte.
Die Verwendung von nur einer Anlage sparte zwar enorme Kosten, bedeutete aber gleichzeitig, dass bei Terminproblemen während des ersten Projekts auch das zweite in Verzug geraten würde.
«Die Termine für die Fertigstellung der Arbeiten an den Flughäfen von Mykonos und Kos waren extrem knapp bemessen», erklärt der Projektleiter Panagiotis Anagnostopoulos. «Wenn wir es nicht geschafft hätten, die Anlage in der uns zur Verfügung stehenden Zeit umzusetzen, hätten wir eine zweite Anlage für das zweite Projekt installieren müssen.»
14 Flughäfen in sieben Monaten
Die Erneuerung der Start- und Landebahnen an den Flughäfen Mykonos und Kos gehört zu den 14 griechischen Flughafenprojekten, die innerhalb von sieben Monaten abgeschlossen werden sollen.
«Die Erweiterung von 14 Flughäfen in einer der beliebtesten Ferienregionen der Welt ist selbst in der Nebensaison eine Herausforderung. Zudem müssen diese Flughäfen saniert und modernisiert werden», erklärt Rolf Klitscher, Projektleiter von Fraport Greece. Diese Konzessionsgesellschaft ist für die nächsten 40 Jahre für Instandhaltung, Betrieb, Verwaltung, Aktualisierung und Entwicklung der 14 regionalen Flughäfen Griechenlands verantwortlich. «Für eine Sanierung können wir die Start- und Landebahnen nur 20 Tage lang schliessen.»
Intrakat ist für die Mischgutherstellung für alle 14 Flughäfen zuständig und nimmt diese Aufgabe sehr ernst. «Die Modernisierung und der Ausbau der 14 inländischen Flughäfen durch Fraport Greece ist eines der grössten Infrastrukturprojekte, die Intrakat bisher ausgeführt hat», bestätigt Christos Papakatsikas, Airside Director von Intrakat.
Auf Mykonos und Kos mussten die Asphaltdecken vollständig erneuert werden. «Auf Mykonos betrug die Produktionsleistung zirka 40’000 Tonnen Asphalt und auf Kos waren es sogar 45’000 Tonnen», führt Papakatsikas weiter aus.
Lesen Sie hier, wie es Intrakat gelungen ist, die knapp bemessenen Fristen einzuhalten und beide Projekte rechtzeitig abzuschliessen.
SCHRITT 1: Schneller Transport
Die ABT QuickBatch basiert auf dem «Container-Prinzip».
Die Kernkomponenten, einschliesslich Trockner-/Filtereinheiten und Mischturmmodule, sind in Gehäusen untergebracht, die gleichzeitig auch als Versandcontainer dienen. Die Komponenten werden in den Grössen 20 oder 40 Fuss gebaut – der gängigen Container-Grösse. Für den Standortwechsel werden die Teile also nur auf das Transportfahrzeug verladen. Die gesamte Anlage lässt sich in 10 Einheiten transportieren.
«Die mobile Container-Anlage lässt sich einfach und kostengünstig umsetzen», erklärt Jannis Charalambidis, Commercial Manager der SPANOS Group I.K.E. – dem Ammann-Vertragshändler für Griechenland. «Die Installation beansprucht nur wenige Tage und man braucht kein Fundament.»
Hinzu kommt ein weiterer Vorteil: Der Transport per Container ist kostengünstiger und die dafür benötigten Versandmethoden sind leichter verfügbar – alles Faktoren, die erhebliche Kosteneinsparungen mit sich bringen, vor allem wenn eine Anlage häufig umgesetzt wird.
SCHRITT 2: Schneller Aufbau
«Für das Umsetzen der Anlage von Mykonos nach Kos hatten wir nur ein kleines Zeitfenster von zwei Wochen», berichtet Klitscher weiter. «In diesem Zeitraum musste die Asphaltanlage abgebaut, verschickt, wiederaufgebaut und in Betrieb genommen werden.»
Anagnostopoulos veranschlagte 10 bis 12 Tage für den Aufbau und 8 bis 10 Tage für den Abbau. «Für den Auf- und Abbau haben wir zwei Kräne und einen kleinen hydraulischen Teleskopkran verwendet, den wir eigentlich gar nicht gebraucht hätten», sagt er.
Die Tatsache, dass kein Fundament benötigt wird, spart Zeit und Geld. Die Komponenten und ihre Anschlüsse sind komplett vormontiert und müssen nur noch zusammengesteckt werden.
SCHRITT 3: Recycling vor Ort
Bei dem Auftrag wurde direkt vor Ort hergestellter Recyclingasphalt (RAP) verwendet. Mit der ABT QuickBatch können hohe Anteile an Ausbauasphalt verarbeitet werden. Zudem nutzte Intrakat eine weitere zeitsparende Methode – den Ammann RSS 120-M. Dieser Schredder verfügt über einen Primär- und Sekundärbrecher sowie eine Siebvorrichtung – und das alles in einer einzigen Maschine.
Der RSS 120-M mit seiner speziell für die RAP-Herstellung patentierten Technologie verarbeitet gemahlenes Gestein ebenso wie Gesteinsbrocken und zerkleinert sie bei niedriger Drehzahl. Das so hergestellte RAP-Material enthält nur geringe Feinstoffanteile, was eine effiziente Einbindung des recycelten Materials in die Heissmineralmischung erleichtert.
Der RSS 120-M ist eine mobile Anlage, die schon 30 Minuten nach Ankunft auf der Baustelle einsatzbereit ist. Das kam Intrakats Anforderungen in Sachen Mobilität, Rüstzeiten, Produktion vor Ort und reduziertem Feinstoffanteil sehr entgegen.
«Der Asphalt wird bereits vor der Produktion aufbereitet. Dafür ist der mobile Schredder RSS 120-M von Ammann eine hervorragende Lösung», lobt Charalambidis.
SCHRITT 4: Produktion maximieren
Während der Arbeiten auf Mykonos und Kos lag die Produktionsleistung der Anlage bei bis zu 150 Tonnen pro Stunde. «Wir hatten nicht geplant, die Nennleistung auszureizen, aber durch die Zugabe von Polymeren kam es zu Verzögerungen, da das Mischgut dann länger gemischt werden muss», erläutert Anagnostopoulos. «Aber wir waren hochzufrieden und die Anlage hat unsere Erwartungen sogar noch übertroffen.»
Als es dann auch noch zu witterungsbedingten Verzögerungen kam, erwies sich die hohe Anlagenleistung als wesentlicher Vorteil. «Die QuickBatch arbeitete sehr produktiv und flexibel», bestätigte Papakatsikas. «Wir konnten die durch Regen und schlechtes Wetter verlorene Zeit durch Doppelschichten und Erhöhen der Anlagenleistung wieder wettmachen.»
«Wir haben das Projekt fristgerecht abgeschlossen, obwohl es wegen des schlechten Wetters zu Verzögerungen gekommen war», freut sich Papakatsikas abschliessend. Es war also ein für alle Beteiligten erfolgreiches Projekt.
Flughafenarbeiten gehören zu den heikelsten Projekten, die ein Bauunternehmen zu bewältigen hat. Die Termine sind extrem knapp bemessen und müssen strikt eingehalten werden. Die Sicherheitsvorkehrungen stellen eine logistische Herausforderung dar. Hinzu kommen andere Unwägbarkeiten wie das Wetter.
Das griechische Bauunternehmen Intrakat hat dieses heikle Szenario nochmals verschärft: Es hat zwei Flughafenprojekte mit eng beieinander liegenden Fertigstellungsterminen übernommen – mit nur einer Asphaltmischanlage. Für die Herstellung der Mischung für den Flughafen von Mykonos verwendete Intrakat die transportoptimierte ABT QuickBatch von Ammann. Danach wurde die Anlage verpackt und in das über 250 Kilometer entfernte Kos verfrachtet, wo sie das Mischgut für ein zweites Flughafenprojekt herstellte.
Die Verwendung von nur einer Anlage sparte zwar enorme Kosten, bedeutete aber gleichzeitig, dass bei Terminproblemen während des ersten Projekts auch das zweite in Verzug geraten würde.
«Die Termine für die Fertigstellung der Arbeiten an den Flughäfen von Mykonos und Kos waren extrem knapp bemessen», erklärt der Projektleiter Panagiotis Anagnostopoulos. «Wenn wir es nicht geschafft hätten, die Anlage in der uns zur Verfügung stehenden Zeit umzusetzen, hätten wir eine zweite Anlage für das zweite Projekt installieren müssen.»
14 Flughäfen in sieben Monaten
Die Erneuerung der Start- und Landebahnen an den Flughäfen Mykonos und Kos gehört zu den 14 griechischen Flughafenprojekten, die innerhalb von sieben Monaten abgeschlossen werden sollen.
«Die Erweiterung von 14 Flughäfen in einer der beliebtesten Ferienregionen der Welt ist selbst in der Nebensaison eine Herausforderung. Zudem müssen diese Flughäfen saniert und modernisiert werden», erklärt Rolf Klitscher, Projektleiter von Fraport Greece. Diese Konzessionsgesellschaft ist für die nächsten 40 Jahre für Instandhaltung, Betrieb, Verwaltung, Aktualisierung und Entwicklung der 14 regionalen Flughäfen Griechenlands verantwortlich. «Für eine Sanierung können wir die Start- und Landebahnen nur 20 Tage lang schliessen.»
Intrakat ist für die Mischgutherstellung für alle 14 Flughäfen zuständig und nimmt diese Aufgabe sehr ernst. «Die Modernisierung und der Ausbau der 14 inländischen Flughäfen durch Fraport Greece ist eines der grössten Infrastrukturprojekte, die Intrakat bisher ausgeführt hat», bestätigt Christos Papakatsikas, Airside Director von Intrakat.
Auf Mykonos und Kos mussten die Asphaltdecken vollständig erneuert werden. «Auf Mykonos betrug die Produktionsleistung zirka 40’000 Tonnen Asphalt und auf Kos waren es sogar 45’000 Tonnen», führt Papakatsikas weiter aus.
Lesen Sie hier, wie es Intrakat gelungen ist, die knapp bemessenen Fristen einzuhalten und beide Projekte rechtzeitig abzuschliessen.
SCHRITT 1: Schneller Transport
Die ABT QuickBatch basiert auf dem «Container-Prinzip».
Die Kernkomponenten, einschliesslich Trockner-/Filtereinheiten und Mischturmmodule, sind in Gehäusen untergebracht, die gleichzeitig auch als Versandcontainer dienen. Die Komponenten werden in den Grössen 20 oder 40 Fuss gebaut – der gängigen Container-Grösse. Für den Standortwechsel werden die Teile also nur auf das Transportfahrzeug verladen. Die gesamte Anlage lässt sich in 10 Einheiten transportieren.
«Die mobile Container-Anlage lässt sich einfach und kostengünstig umsetzen», erklärt Jannis Charalambidis, Commercial Manager der SPANOS Group I.K.E. – dem Ammann-Vertragshändler für Griechenland. «Die Installation beansprucht nur wenige Tage und man braucht kein Fundament.»
Hinzu kommt ein weiterer Vorteil: Der Transport per Container ist kostengünstiger und die dafür benötigten Versandmethoden sind leichter verfügbar – alles Faktoren, die erhebliche Kosteneinsparungen mit sich bringen, vor allem wenn eine Anlage häufig umgesetzt wird.
SCHRITT 2: Schneller Aufbau
«Für das Umsetzen der Anlage von Mykonos nach Kos hatten wir nur ein kleines Zeitfenster von zwei Wochen», berichtet Klitscher weiter. «In diesem Zeitraum musste die Asphaltanlage abgebaut, verschickt, wiederaufgebaut und in Betrieb genommen werden.»
Anagnostopoulos veranschlagte 10 bis 12 Tage für den Aufbau und 8 bis 10 Tage für den Abbau. «Für den Auf- und Abbau haben wir zwei Kräne und einen kleinen hydraulischen Teleskopkran verwendet, den wir eigentlich gar nicht gebraucht hätten», sagt er.
Die Tatsache, dass kein Fundament benötigt wird, spart Zeit und Geld. Die Komponenten und ihre Anschlüsse sind komplett vormontiert und müssen nur noch zusammengesteckt werden.
SCHRITT 3: Recycling vor Ort
Bei dem Auftrag wurde direkt vor Ort hergestellter Recyclingasphalt (RAP) verwendet. Mit der ABT QuickBatch können hohe Anteile an Ausbauasphalt verarbeitet werden. Zudem nutzte Intrakat eine weitere zeitsparende Methode – den Ammann RSS 120-M. Dieser Schredder verfügt über einen Primär- und Sekundärbrecher sowie eine Siebvorrichtung – und das alles in einer einzigen Maschine.
Der RSS 120-M mit seiner speziell für die RAP-Herstellung patentierten Technologie verarbeitet gemahlenes Gestein ebenso wie Gesteinsbrocken und zerkleinert sie bei niedriger Drehzahl. Das so hergestellte RAP-Material enthält nur geringe Feinstoffanteile, was eine effiziente Einbindung des recycelten Materials in die Heissmineralmischung erleichtert.
Der RSS 120-M ist eine mobile Anlage, die schon 30 Minuten nach Ankunft auf der Baustelle einsatzbereit ist. Das kam Intrakats Anforderungen in Sachen Mobilität, Rüstzeiten, Produktion vor Ort und reduziertem Feinstoffanteil sehr entgegen.
«Der Asphalt wird bereits vor der Produktion aufbereitet. Dafür ist der mobile Schredder RSS 120-M von Ammann eine hervorragende Lösung», lobt Charalambidis.
SCHRITT 4: Produktion maximieren
Während der Arbeiten auf Mykonos und Kos lag die Produktionsleistung der Anlage bei bis zu 150 Tonnen pro Stunde. «Wir hatten nicht geplant, die Nennleistung auszureizen, aber durch die Zugabe von Polymeren kam es zu Verzögerungen, da das Mischgut dann länger gemischt werden muss», erläutert Anagnostopoulos. «Aber wir waren hochzufrieden und die Anlage hat unsere Erwartungen sogar noch übertroffen.»
Als es dann auch noch zu witterungsbedingten Verzögerungen kam, erwies sich die hohe Anlagenleistung als wesentlicher Vorteil. «Die QuickBatch arbeitete sehr produktiv und flexibel», bestätigte Papakatsikas. «Wir konnten die durch Regen und schlechtes Wetter verlorene Zeit durch Doppelschichten und Erhöhen der Anlagenleistung wieder wettmachen.»
«Wir haben das Projekt fristgerecht abgeschlossen, obwohl es wegen des schlechten Wetters zu Verzögerungen gekommen war», freut sich Papakatsikas abschliessend. Es war also ein für alle Beteiligten erfolgreiches Projekt.

Kontakt-Formular
Online-Termin vereinbaren
Setzen Sie sich mit uns in Verbindung, um einen Vertriebsmitarbeiter in Ihrer Nähe zu treffen
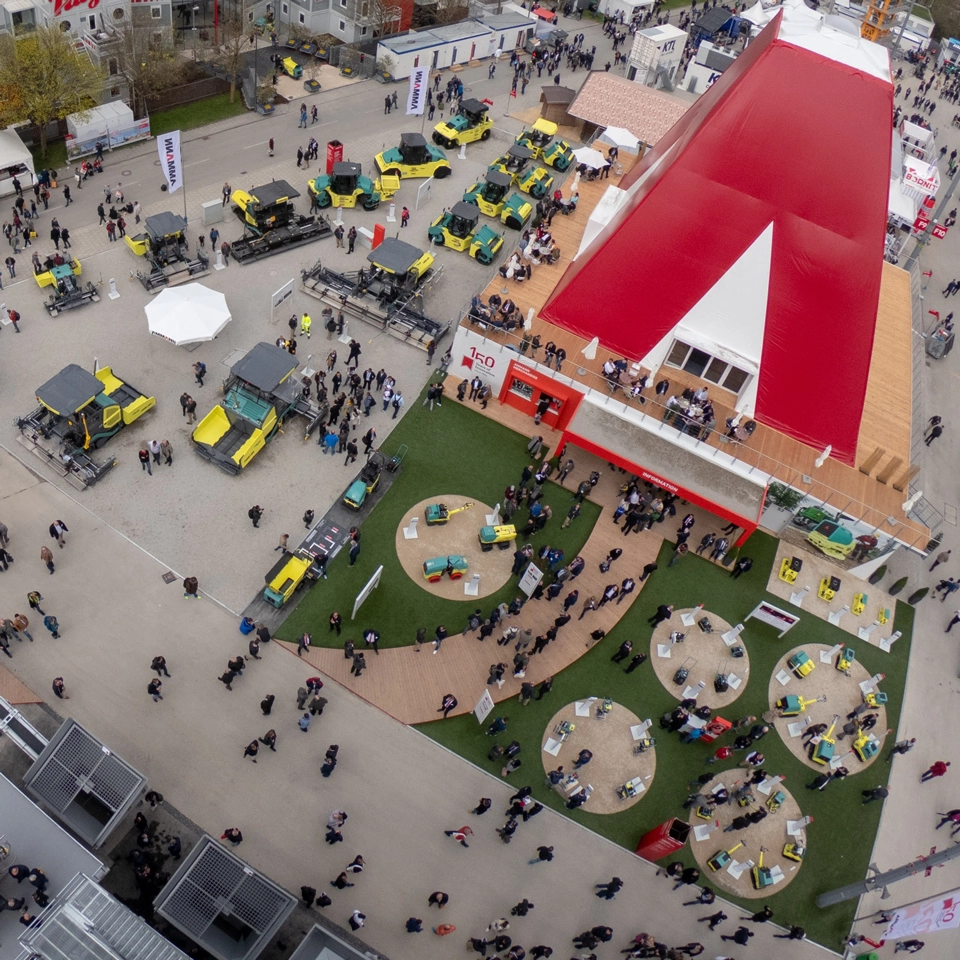