Asphalt Plants
Technology
7 Steps to Making Your Asphalt Plant Last
98 Per Cent Uptime for Colas’ Ammann Facility
Despite challenging conditions, an asphalt plant owned by Colas Ltd. has continued to achieve a 98 per cent availability rate despite operating in an extremely tough environment.
“There is a view of the English Channel from the top of the plant tower – that’s how close we are to the water,” said John Hudson, an engineer and site foreman at the plant in Carnsew Quarry, Cornwall, England. “We have a lot of moisture in the air.”
The conditions can get a bit raw, but they aren’t the only challenge facing Hudson and his colleagues, who operate and maintain the asphalt plant. “Plants are an investment, and you have to maximise the return,” he said. “By ensuring the plant lasts, you can get the most out of that investment.”
How do Hudson and his colleagues make the plant last?
1. Demand quality when purchasing the plant. Hudson works for UK-based Colas Ltd., which is part of Colas SA, a major international group with headquarters in France. He and others at the local site encouraged the purchase of an Ammann Uniglobe 200 Batch Plant when the decision was being made a decade ago. “Ammann was able to take our specifications and deliver the right fit,” Hudson said. “They came up with a design that perfectly matched our needs. The plants also have durability, and the pieces fit together to limit wear.” Hudson’s bottom line: Choose a superior product, because all the maintenance in the world can’t make a poorly manufactured plant last.
2. Buy quality replacement parts. “You don’t save money when you use cheap replacements,” Hudson said. “That’s why we buy parts directly from the manufacturer (Ammann). Parts that fit perfectly reduce wear, last longer and therefore reduce cost.”
3. Walk around – a lot. Hudson and his team have their regular inspections of dryers, the baghouse and other commonsense locations. Yet they also look for wear in less obvious places. Have abrasive aggregates worn down various components of the elevator? Do materials routinely spill in a specific location, which can take a toll over time? “If you can’t find something, you’re not looking hard enough,” Hudson said.
4. Watch what’s moving. “There are a lot of moving parts to an asphalt plant,” Hudson said. “There are rollers for conveyors and gearboxes that drive the conveyors. Pay special attention to those moving parts. Moving causes wear and, if one of the moving parts breaks down, it can often damage others.”
5. Schedule a regular maintenance day. “The reason the plant doesn’t look 10 years old is because we maintain it every weekend,” Hudson said. “I think the saving grace of any asphalt plant is preventive maintenance.” Saturday is the maintenance day for Hudson and his colleagues. Tasks include maintenance and repairs, as well as inspections that often uncover work for the following weekend. “If a problem is found, it’s not ignored,” Hudson said.
6. Utilise outside resources. Hudson’s team does most of the maintenance, but they also turn to the manufacturer for certain specialised services. “Right now we have Ammann here servicing the burners,” Hudson said. “We have them do that every six months.” The manufacturer has tools and experience that Hudson could obtain, but he realizes some efforts are best left to the specialists. “There is a lot that goes into that service he said.
7. Think through the process in advance. When planning a repair for the upcoming weekend, Hudson takes a careful look at the tools that will be needed and the processes that are most likely to be successful. Depending on the repair, he sometimes designs tools that ultimately save considerable time. “You would be surprised how many frustrations you can avoid by looking and thinking through as many details as possible in advance.”
That approach – and the others – means more maintenance and repairs are completed in a timely manner. And that leaves time for … more maintenance and repairs, which in the end ensures the plant lasts longer.
Despite challenging conditions, an asphalt plant owned by Colas Ltd. has continued to achieve a 98 per cent availability rate despite operating in an extremely tough environment.
“There is a view of the English Channel from the top of the plant tower – that’s how close we are to the water,” said John Hudson, an engineer and site foreman at the plant in Carnsew Quarry, Cornwall, England. “We have a lot of moisture in the air.”
The conditions can get a bit raw, but they aren’t the only challenge facing Hudson and his colleagues, who operate and maintain the asphalt plant. “Plants are an investment, and you have to maximise the return,” he said. “By ensuring the plant lasts, you can get the most out of that investment.”
How do Hudson and his colleagues make the plant last?
1. Demand quality when purchasing the plant. Hudson works for UK-based Colas Ltd., which is part of Colas SA, a major international group with headquarters in France. He and others at the local site encouraged the purchase of an Ammann Uniglobe 200 Batch Plant when the decision was being made a decade ago. “Ammann was able to take our specifications and deliver the right fit,” Hudson said. “They came up with a design that perfectly matched our needs. The plants also have durability, and the pieces fit together to limit wear.” Hudson’s bottom line: Choose a superior product, because all the maintenance in the world can’t make a poorly manufactured plant last.
2. Buy quality replacement parts. “You don’t save money when you use cheap replacements,” Hudson said. “That’s why we buy parts directly from the manufacturer (Ammann). Parts that fit perfectly reduce wear, last longer and therefore reduce cost.”
3. Walk around – a lot. Hudson and his team have their regular inspections of dryers, the baghouse and other commonsense locations. Yet they also look for wear in less obvious places. Have abrasive aggregates worn down various components of the elevator? Do materials routinely spill in a specific location, which can take a toll over time? “If you can’t find something, you’re not looking hard enough,” Hudson said.
4. Watch what’s moving. “There are a lot of moving parts to an asphalt plant,” Hudson said. “There are rollers for conveyors and gearboxes that drive the conveyors. Pay special attention to those moving parts. Moving causes wear and, if one of the moving parts breaks down, it can often damage others.”
5. Schedule a regular maintenance day. “The reason the plant doesn’t look 10 years old is because we maintain it every weekend,” Hudson said. “I think the saving grace of any asphalt plant is preventive maintenance.” Saturday is the maintenance day for Hudson and his colleagues. Tasks include maintenance and repairs, as well as inspections that often uncover work for the following weekend. “If a problem is found, it’s not ignored,” Hudson said.
6. Utilise outside resources. Hudson’s team does most of the maintenance, but they also turn to the manufacturer for certain specialised services. “Right now we have Ammann here servicing the burners,” Hudson said. “We have them do that every six months.” The manufacturer has tools and experience that Hudson could obtain, but he realizes some efforts are best left to the specialists. “There is a lot that goes into that service he said.
7. Think through the process in advance. When planning a repair for the upcoming weekend, Hudson takes a careful look at the tools that will be needed and the processes that are most likely to be successful. Depending on the repair, he sometimes designs tools that ultimately save considerable time. “You would be surprised how many frustrations you can avoid by looking and thinking through as many details as possible in advance.”
That approach – and the others – means more maintenance and repairs are completed in a timely manner. And that leaves time for … more maintenance and repairs, which in the end ensures the plant lasts longer.

Contact Form
Schedule online meeting
Get in touch with us to meet a sales representative near you
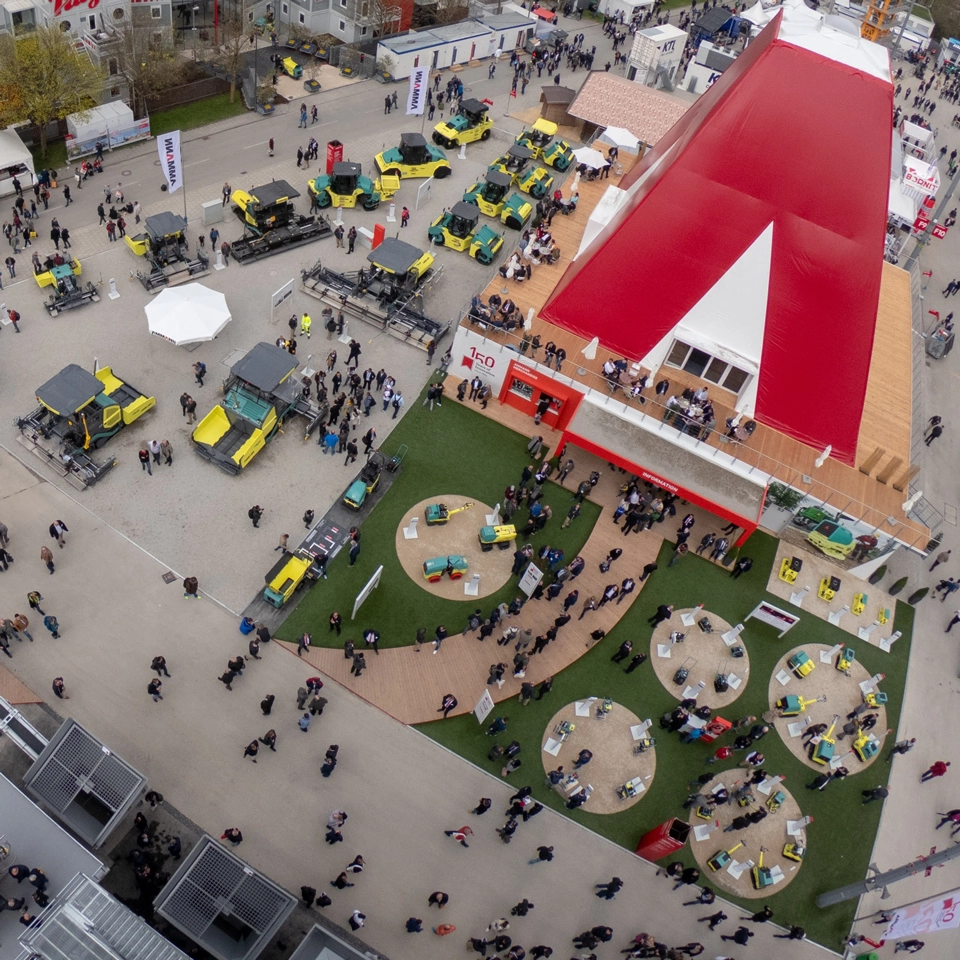