Asphalt Plants
Technology
Changing the Mindset of the Industry
Firm Strives to be Recycling Leader in North America
Ryan Smith began his search for the ultimate recycling asphalt-mixing plant a number of years ago. Exhaustive research led him to Ammann.
“Four years ago, we searched for a solution that would use the byproduct that is created when reconstructing roads,” said Smith, chief executive officer at Columbus, Ohio-based RAP Management. “In November of 2016, we signed a contract and made an acquisition to buy an Ammann High Recycling Technology asphalt plant – the first of its kind on this continent.”
Smith had high expectations for the plant. He believed it would help his business become an environmental leader in North America.
“The purpose of RAP Management is to manage recycled asphalt product,” Smith said. “Our goal is to change the mindset of our industry. With this valuable byproduct that’s generated from reconstructing roads, we can create high-quality asphalt products at a low cost.”
Smith knew from the beginning that he had to offer customers more than a green product – he had to provide quality and cost-effectiveness, too. Smith shared some of the key steps he took to ensure he found the optimal plant.
Explore all options. Smith’s research was extensive. He and his team visited a number of trade shows to review existing products – and these encounters sometimes gave them a glimpse of what might be coming next. The trade shows offered an opportunity to easily compare and contrast plants on the market. Next, the team visited facilities in operation to see how the products performed on the jobsite.
Find the latest, most innovative technology. Changing the industry requires innovation. That’s one of the reasons Smith chose the Ammann ABP HRT. It relies on patented technology that enables the use of high percentages of RAP.
“Ammann’s high-recycling technology works by heating some of the recycled material we’re adding to our mix,” Smith said. “The parallel dryer, which sits on top of the plant, allows us to add energy in an efficient manner, heating some of the recycled material, increasing the amount of RAP we add to our mix, and reducing the super-heating requirement for the virgin aggregate necessary to meet any specification.”
A green product must still be superior. There is no place in the market for a product that is green but lacking in quality. “The asphalt we’re producing from the plant is as good if not better than our competitors’ products,” Smith said.
The plant also delivers the production Smith needs. “We can produce anywhere from 175 to 280 (U.S.) tons per hour, depending on demand by customers and the recycle content of the mix,” Smith said.
Meet customers’ specific needs. Customers often require specialty mixes, and the plant must be able to create them. “We are able with this facility to properly and precisely add whatever is necessary to meet any given specification,” Smith said. “The plant can precisely dose small quantities of additives to meet whatever performance grade of job-mix formula is necessary.”
The money matters. If cost and quality were equal, most customers would choose a green product. But few businesses can afford to spend more for the sole purpose of using high percentages of RAP. The Ammann plant and its ability to use RAP leads to significant cost savings during the production process, which provides incentive for customers to pursue environmentally friendly solutions.
“Our business is sustainable not because we recycle, but by recycling we lower our cost to manufacture – and that’s savings we can pass onto our customers,” Smith said.
The control system brings it all together. The Ammann HRT utilises Ammann’s proprietary as1 Control System. “It’s essential to operating the facility,” Smith said. “It’s easy to run, intuitive and very robust and comprehensive.”
The data it collects and processes is crucial, too. “We evaluate down to the penny,” Smith said. “Utilising the information that the as1 Control System collects about the asphalt products we produce is extremely valuable to our business and gives us the resources necessary to assure we are meeting our targets and operating a successful business.”
Leverage all the value the plant brings. Smith said representatives of Ammann provided great support during the installation and start-up of the plant. Technicians and production experts remained on-site to ensure proper understanding of the plant and its functions.
The support continues to this day. RAP Management has access to Ammann’s 24-hour assistance hotline. The Ammann after-sales team can even control the plant remotely if need be.
“Ammann has supported us every step of the way, to the extent I’ve created new friends all around the world who provide me help on a daily basis, ensuring we have the right tools to successfully operate the equipment and, in turn, operate a successful business,” Smith said.
While following these key guidelines, Smith never lost sight of the reason he went into the business: to transform a waste product into valuable asphalt mix, thereby improving the world around him.
“We’re producing asphalt with an average recycled content above 60 per cent,” he said. “In the U.S., our industry recycles 20 percent, so we’re recycling three times the recycle content of our competitors.
“The benefit to our customers is a high-quality, very workable asphalt product at a low cost. The benefit to our community is highly engineered roads that are built to last – and tons of waste kept out of landfills.”
Ryan Smith began his search for the ultimate recycling asphalt-mixing plant a number of years ago. Exhaustive research led him to Ammann.
“Four years ago, we searched for a solution that would use the byproduct that is created when reconstructing roads,” said Smith, chief executive officer at Columbus, Ohio-based RAP Management. “In November of 2016, we signed a contract and made an acquisition to buy an Ammann High Recycling Technology asphalt plant – the first of its kind on this continent.”
Smith had high expectations for the plant. He believed it would help his business become an environmental leader in North America.
“The purpose of RAP Management is to manage recycled asphalt product,” Smith said. “Our goal is to change the mindset of our industry. With this valuable byproduct that’s generated from reconstructing roads, we can create high-quality asphalt products at a low cost.”
Smith knew from the beginning that he had to offer customers more than a green product – he had to provide quality and cost-effectiveness, too. Smith shared some of the key steps he took to ensure he found the optimal plant.
Explore all options. Smith’s research was extensive. He and his team visited a number of trade shows to review existing products – and these encounters sometimes gave them a glimpse of what might be coming next. The trade shows offered an opportunity to easily compare and contrast plants on the market. Next, the team visited facilities in operation to see how the products performed on the jobsite.
Find the latest, most innovative technology. Changing the industry requires innovation. That’s one of the reasons Smith chose the Ammann ABP HRT. It relies on patented technology that enables the use of high percentages of RAP.
“Ammann’s high-recycling technology works by heating some of the recycled material we’re adding to our mix,” Smith said. “The parallel dryer, which sits on top of the plant, allows us to add energy in an efficient manner, heating some of the recycled material, increasing the amount of RAP we add to our mix, and reducing the super-heating requirement for the virgin aggregate necessary to meet any specification.”
A green product must still be superior. There is no place in the market for a product that is green but lacking in quality. “The asphalt we’re producing from the plant is as good if not better than our competitors’ products,” Smith said.
The plant also delivers the production Smith needs. “We can produce anywhere from 175 to 280 (U.S.) tons per hour, depending on demand by customers and the recycle content of the mix,” Smith said.
Meet customers’ specific needs. Customers often require specialty mixes, and the plant must be able to create them. “We are able with this facility to properly and precisely add whatever is necessary to meet any given specification,” Smith said. “The plant can precisely dose small quantities of additives to meet whatever performance grade of job-mix formula is necessary.”
The money matters. If cost and quality were equal, most customers would choose a green product. But few businesses can afford to spend more for the sole purpose of using high percentages of RAP. The Ammann plant and its ability to use RAP leads to significant cost savings during the production process, which provides incentive for customers to pursue environmentally friendly solutions.
“Our business is sustainable not because we recycle, but by recycling we lower our cost to manufacture – and that’s savings we can pass onto our customers,” Smith said.
The control system brings it all together. The Ammann HRT utilises Ammann’s proprietary as1 Control System. “It’s essential to operating the facility,” Smith said. “It’s easy to run, intuitive and very robust and comprehensive.”
The data it collects and processes is crucial, too. “We evaluate down to the penny,” Smith said. “Utilising the information that the as1 Control System collects about the asphalt products we produce is extremely valuable to our business and gives us the resources necessary to assure we are meeting our targets and operating a successful business.”
Leverage all the value the plant brings. Smith said representatives of Ammann provided great support during the installation and start-up of the plant. Technicians and production experts remained on-site to ensure proper understanding of the plant and its functions.
The support continues to this day. RAP Management has access to Ammann’s 24-hour assistance hotline. The Ammann after-sales team can even control the plant remotely if need be.
“Ammann has supported us every step of the way, to the extent I’ve created new friends all around the world who provide me help on a daily basis, ensuring we have the right tools to successfully operate the equipment and, in turn, operate a successful business,” Smith said.
While following these key guidelines, Smith never lost sight of the reason he went into the business: to transform a waste product into valuable asphalt mix, thereby improving the world around him.
“We’re producing asphalt with an average recycled content above 60 per cent,” he said. “In the U.S., our industry recycles 20 percent, so we’re recycling three times the recycle content of our competitors.
“The benefit to our customers is a high-quality, very workable asphalt product at a low cost. The benefit to our community is highly engineered roads that are built to last – and tons of waste kept out of landfills.”

Contact Form
Schedule online meeting
Get in touch with us to meet a sales representative near you
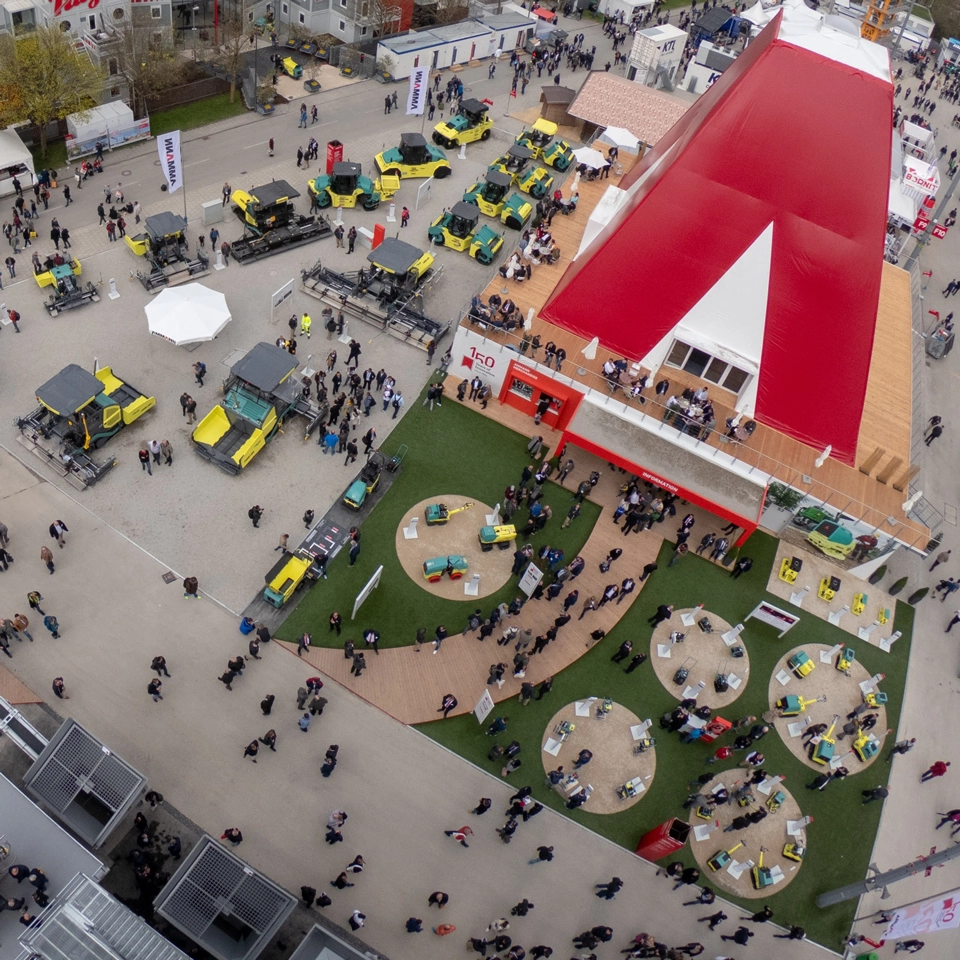